Delivery Tracking: The 5 Mistakes That Wreck Your Schedules (and How to Avoid Them)
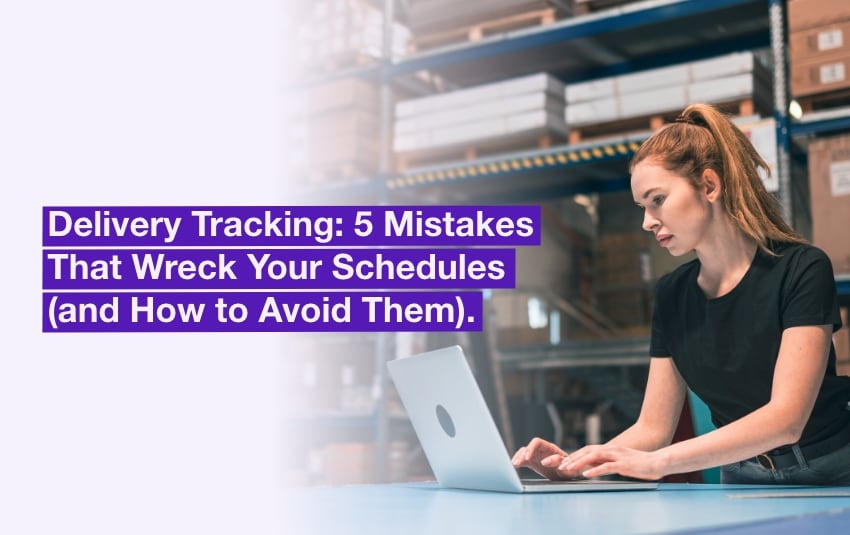
Delivery delays, unhappy customers, overwhelmed teams… The day has barely begun when an angry customer calls: their order still hasn’t arrived. The driver is stuck in traffic, and there’s no up-to-date information available. The result? A customer service team under pressure, a poor customer experience, and a supply chain that’s falling apart.
Unfortunately, this kind of scenario is still common in companies where the delivery tracking system is rigid, siloed, and disconnected from real-world operations. Yet with structured, connected, and data-driven planning, it’s entirely possible to avoid such breakdowns—and even turn logistics into a competitive advantage.
Today, managing delivery routes, tracking parcels in real time, and anticipating disruptions requires much more than just an Excel spreadsheet. Effective logistics planning depends on collaborative tools, continuously updated data, and an organization agile enough to adapt to on-the-ground changes.
In this article, we’ll review the 5 most common delivery planning mistakes—and more importantly, how to fix them with the best practices to adopt in 2025.
Table of contents:
- Understanding Delivery Tracking Schedules
- The 5 Common Mistakes in Delivery Tracking Planning
- Best Practices for Effective Delivery Tracking Planning in 2025
Understanding Delivery Tracking Schedules
Delivery tracking planning is no longer just about assigning time slots on a map or allocating parcels to drivers. It has evolved into a comprehensive process that encompasses logistics planning, real-time delivery tracking, team coordination, and continuous performance improvement.
The challenge is no longer just delivering a parcel to its destination: it must arrive at the right time, in the right place, with the right information—and ideally, on the first try.
End-to-End Management
In practice, an effective delivery schedule starts well before the first parcel is loaded and continues long after it’s handed over to the customer. Here are the key elements it should include:
- Route optimization (routes, time slots, stop sequences).
- Anticipation of disruptions (traffic, weather, absences, cancellations).
- Smooth communication between all departments (logistics, field teams, customer service).
- Real-time tracking of every step, right through to proof of delivery.
- Data analysis to refine and forecast future delivery routes.
This level of expectation has become the norm. Customers want to know where their parcel is, when it will arrive, and have the option to reschedule the delivery if needed.
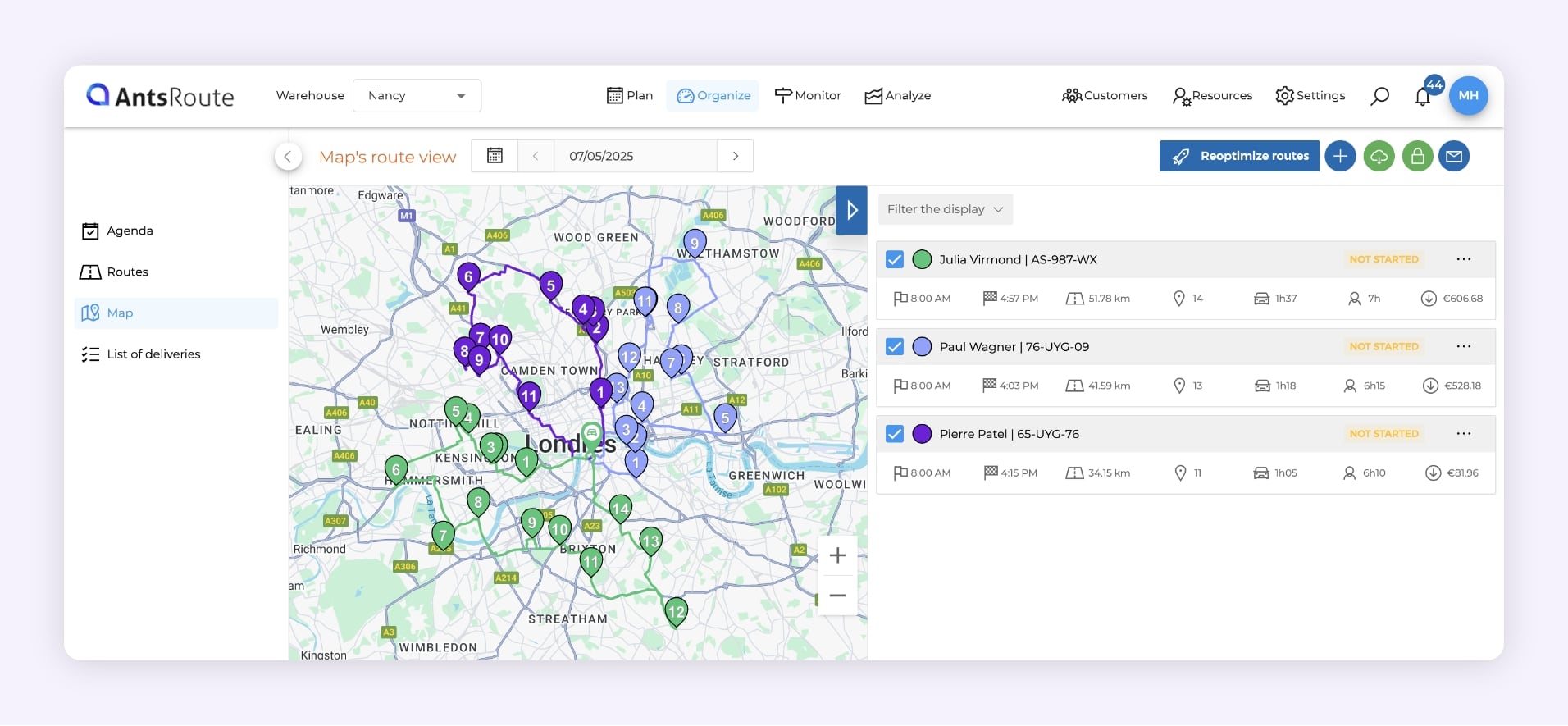
Route optimization with AntsRoute.
A Strategic Challenge for Your Business
For transport, logistics, or home delivery companies, poor planning quickly leads to:
- A chain reaction of delays.
- Unhappy customers.
- A flood of calls to customer service.
- Extra costs in fuel and overtime.
Conversely, well-designed delivery planning makes it possible to:
- Reduce lead times and logistics costs.
- Strengthen customer trust.
- Increase first-attempt delivery success rates.
- Manage operations using reliable logistics KPIs.
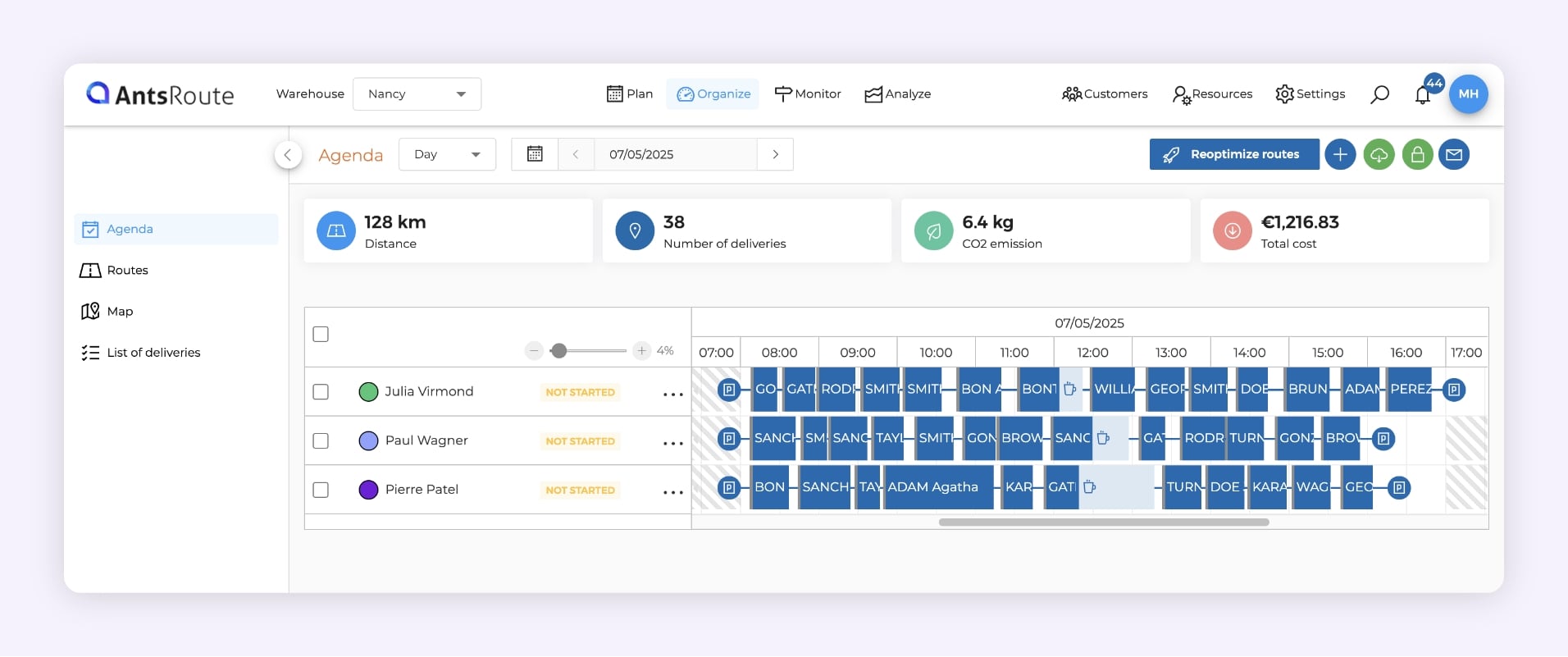
Optimizing a delivery schedule with AntsRoute.
A Data-Driven Process… Powered by the Right Tools
The good news? Manual management is no longer necessary. Today’s top-performing companies rely on delivery planning software that can:
- Geolocate vehicles and track routes in real time.
- Automatically recalculate routes based on unexpected events.
- Collect proof of delivery (signature, photo, PIN code).
- Centralize data into clear, accessible dashboards.
Say Goodbye to Rigid, Time-Consuming Excel Files: Make Way for Scalable Solutions. These modern tools sync with your business systems (ERP, TMS, CRM) and adjust in real time.
Whether you’re delivering meals, medication, furniture, or technical equipment, your ability to ensure delivery traceability and respond effectively to unexpected events makes all the difference—provided, of course, you avoid the common mistakes that still too often hurt productivity and customer satisfaction.
The 5 Common Mistakes in Delivery Tracking Planning
Good planning means avoiding unpleasant surprises. Yet many companies still make common mistakes that hurt their logistics efficiency.
Here are the 5 most frequent pitfalls in delivery tracking planning:
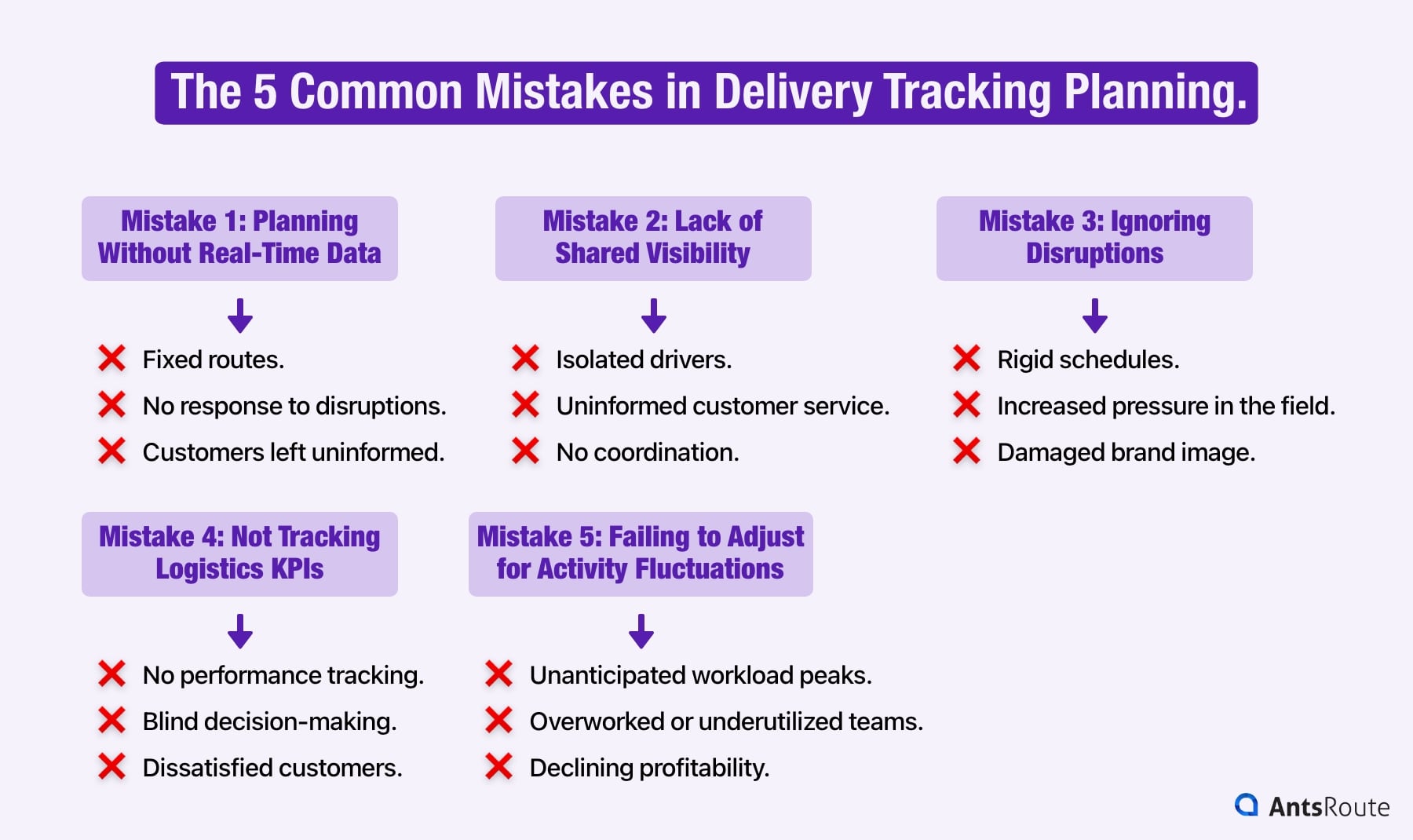
The 5 common mistakes in delivery tracking planning.
Mistake 1: Planning Without Real-Time Data
Planning a delivery day without up-to-date data is like flying blind. You create a route assuming everything will go smoothly… while in reality, unexpected events are common: traffic jams, absences, rescheduling.
Without real-time visibility, your teams can’t:
- React quickly to traffic disruptions.
- Reschedule routes based on incidents.
- Notify customers in case of time changes.
The result: Unanticipated delays, wasted time, overwhelmed customer service… and plummeting customer satisfaction.
Indeed, a rigid schedule deprives your business of:
- Flexibility: It’s impossible to reschedule a stop on the fly.
- Reactivity: Decisions are made without clear visibility.
- Effective management: Logistics managers lack concrete data.
- Customer trust: How can you reassure customers if you can’t give them a realistic estimated time of arrival?
Mistake 2: Failing to Centralize Visibility Across Teams
Logistics manager, driver, customer service—everyone is working hard, but each in their own silo. The manager plans the routes using one software, the driver checks them on their phone, while customer service tries to handle calls without knowing what’s really happening on the ground.
This fragmentation of information creates a real logistics blind spot. The consequences are immediate:
- Delays aren’t reported in time.
- Customer service gives approximate or incorrect time estimates.
- The driver handles unexpected issues alone, with no support or guidance.
- The customer, poorly informed, loses trust in the service.
In short: Dispersed information, frequent misunderstandings, and a general sense of confusion—for both the team and the customers.
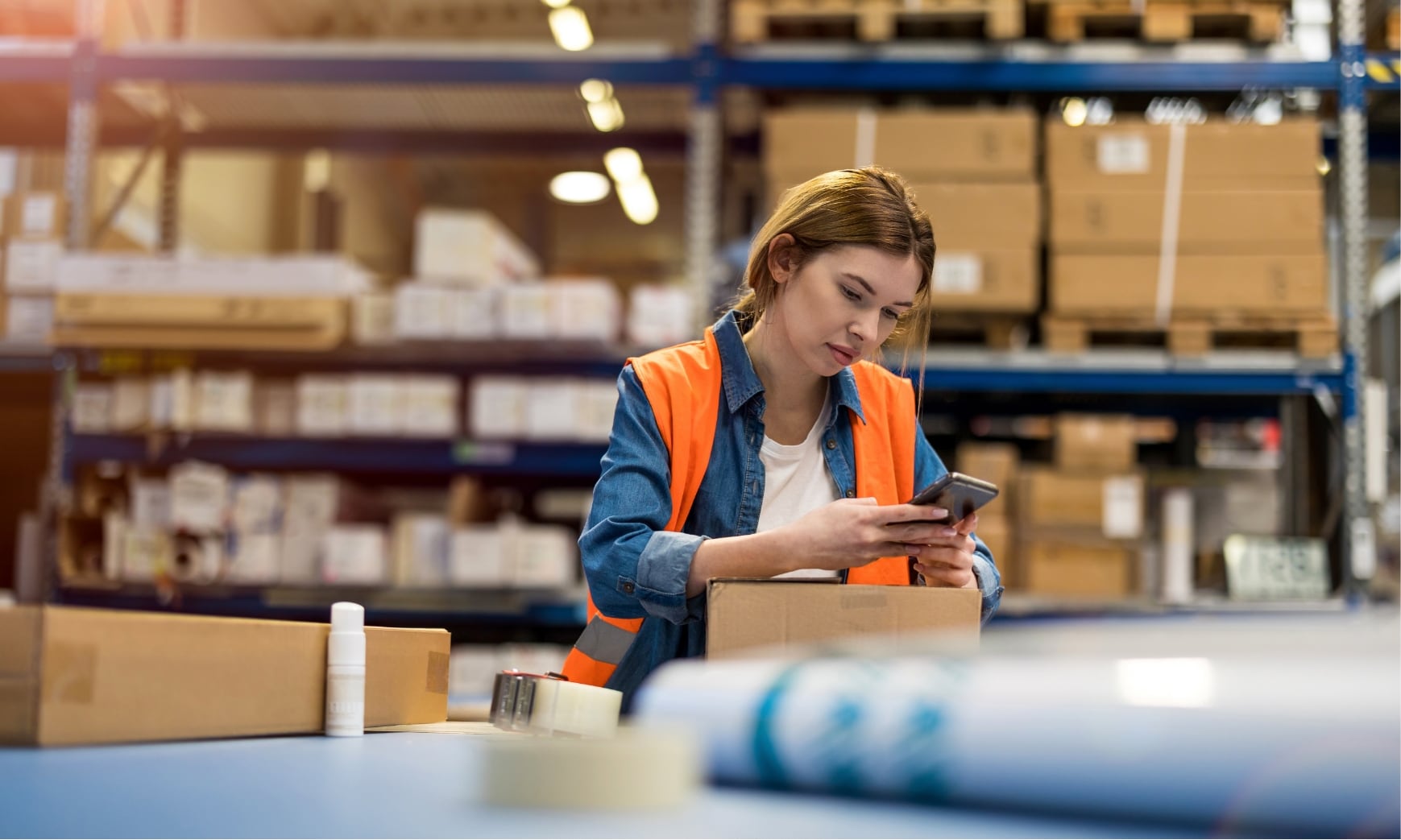
Delivery planning software makes it possible to quickly adapt to on-the-ground disruptions.
Mistake 3: Ignoring External Disruptions
Accidents, roadworks, strikes, unpredictable weather, absent customers… In logistics, disruptions are the rule, not the exception. Yet many companies still plan their deliveries as if every day will go off without a hitch.
The result: At the slightest disruption, the schedule collapses like a house of cards. Delays pile up, drivers are forced to improvise, and customer service is overwhelmed with complaints.
A schedule that can’t adapt leads to:
- Disorganized routes as soon as an event disrupts the planned itinerary.
- Mental overload for drivers, left to fend for themselves in case of problems.
- Nearly zero responsiveness, as adjustments are made reactively and in a rush.
- A damaged brand image due to repeated, unexplained delays.
Mistake 4: Failing to Track or Use Logistics KPIs
A late delivery, an unhappy customer, a route that took longer than expected… These aren’t always just isolated incidents. Without reliable performance indicators (KPIs), it’s hard to know whether these are exceptions—or warning signs.
Not tracking your KPIs is like driving without a dashboard: you’re moving forward, but you have no idea if you’re on the right path. As a result, your planning remains vague and impossible to optimize:
- No visibility into actual performance: It’s hard to assess how efficient your routes really are.
- Blind decision-making: Adjustments are based on guesswork, not facts.
- Unsatisfied customers: Without data, you can’t explain delays—or improve them.
Mistake 5: Not Adapting the Schedule to Activity Fluctuations
Using the same delivery plan in the middle of summer as during the holiday season? Organizing Monday routes the same way as Friday’s? If your delivery schedule stays the same all year round, you’re setting yourself up for serious imbalances. The reality is that logistics activity is anything but linear. It varies with seasons, sales events, customer habits, public holidays—even the weather.
A schedule that can’t adjust to these fluctuations results in:
- Overloaded teams during peak demand periods.
- Underused resources during slow periods.
- Deliveries that are late or rushed.
- Decreased profitability and more frequent mistakes
In short: An organization that reacts to events instead of anticipating them.
Best Practices for Effective Delivery Tracking Planning in 2025
Fixing mistakes is good. But implementing a sustainable, scalable strategy is even better. Here are the best practices to adopt to turn your logistics planning into a true performance driver.
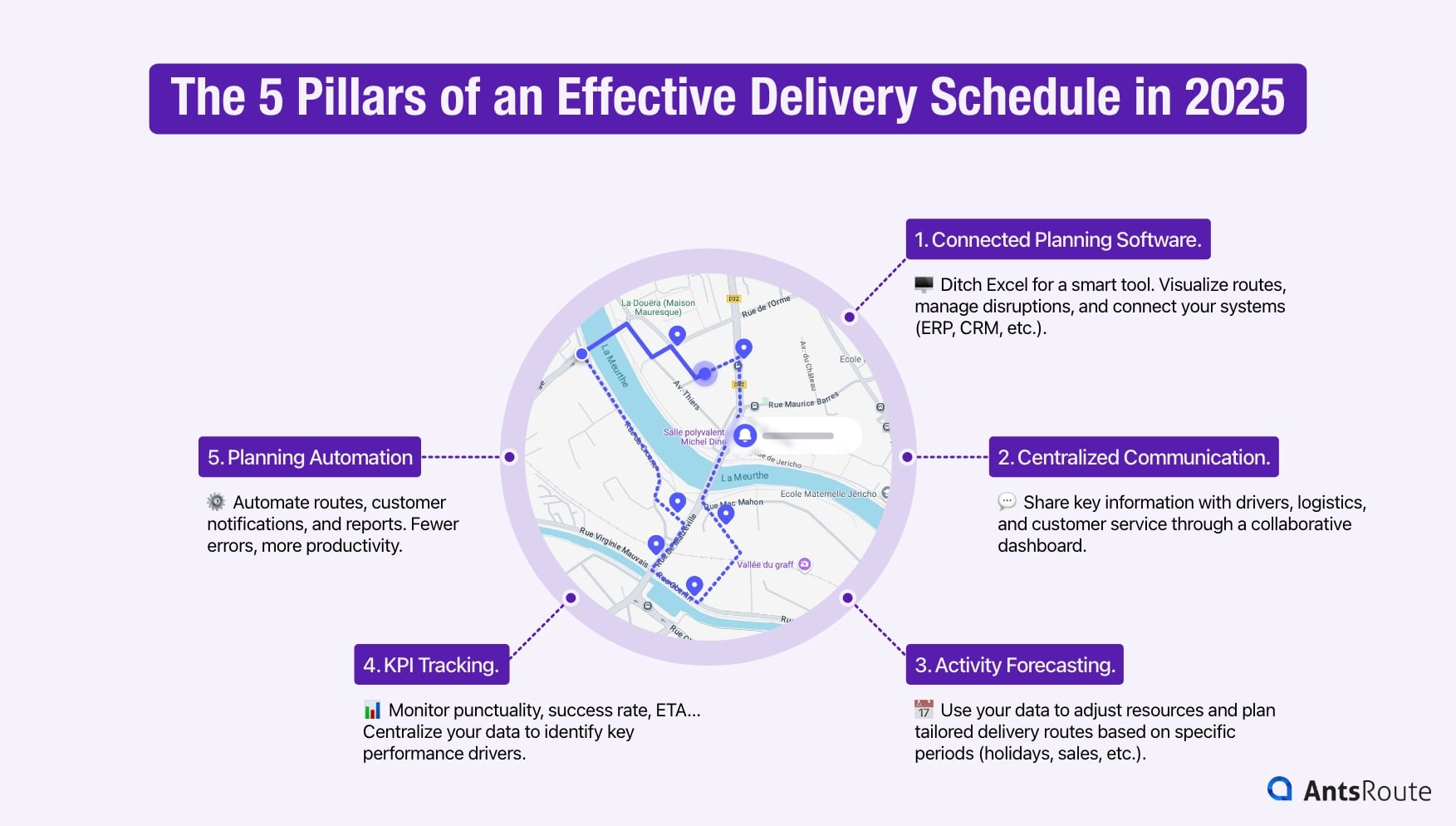
The 5 pillars of an effective delivery schedule.
1. Equip Yourself with Connected Planning Software
Say goodbye to static Excel schedules. To boost responsiveness, choose delivery planning software that can:
- Visualize routes in real time with geolocation.
- Automatically adjust routes based on traffic or cancellations.
- Update delivery statuses with a single click.
- Sync with your business tools (ERP, CRM, TMS).
- Automatically notify your customers.
☝️ A tool like AntsRoute not only automates route building by taking business constraints into account (time windows, vehicle capacity, delivery zones), but also enables real-time delivery tracking. The result? 50% fewer calls to customer service, improved efficiency, greater reliability… and a significant increase in on-time delivery rate, according to the logistics director at Margain Marée.
2. Centralize Communication for Collaborative Management
A solid logistics plan relies on a team moving in the same direction. Logistics managers, drivers, and customer service must all share the same visibility—at the same time. This requires:
- A shared dashboard displaying real-time delivery progress.
- Automatic notifications for delays, deliveries, or changes.
- A messaging system or comment space to streamline communication, with the ability to attach photos or documents.
☝️ At Ferme Saint-André, drivers always photograph the fresh produce baskets left at drop-off points. These images are integrated into the tracking system and accessible to customer service— a real advantage in case of disputes.
3. Integrate Activity Forecasting into Your Planning
Anticipation prevents disorganization. To align your resources with delivery volumes, rely on historical data and predictive algorithms:
- Identify seasonal peaks (holidays, sales events, back-to-school, etc.)
- Adjust your resources in advance: vehicles, drivers, time slots.
- Create specific route models based on time periods or delivery zones.
This results in schedules that are realistic, balanced, and more readily accepted by field teams.
☝️ “Using [AntsRoute] has saved us 40 to 50% in delivery time,” says Maïté Galou, founder of Licorne Express, “and it also allows us to handle larger volumes on already high-pressure days like Mother’s Day or Christmas.”
4. Manage Your Performance with the Right KPIs
Without reliable indicators, improvement is difficult. But there’s no need to measure everything—focus on the logistics KPIs that truly matter. Here are the essentials for evaluating your planning:
- On-time delivery rate.
- Average gap between the estimated time of arrival (ETA) and the actual delivery time
- First-attempt delivery success rate.
- Average time per route.
- Customer satisfaction level.
A quick tip: centralize this data in clear, real-time dashboards. This will help you quickly identify strengths, areas for improvement, and make informed, data-driven decisions.
☝️ At Ferme Saint-André, “the data provided by the software helps us better understand the causes of these discrepancies, so we can modify certain routes and organize ourselves more effectively,” explains Véronique Pfister, their technical supervisor.
5. Automate to Save Time and Boost Efficiency
Automating your delivery planning brings significant time savings on a daily basis. It enables you to:
- Generate delivery routes in just a few clicks based on your constraints and priorities.
- Automatically send notifications to customers.
- Respond to disruptions in real time.
- Produce operational reports without manual data entry.
By combining the right tools, reliable data, and seamless collaboration, you can turn your logistics planning into a strategic asset for 2025. Smarter planning. More agile. And above all… far more profitable.
Looking to improve your delivery operations, reduce delays, and automate your planning — without adding complexity for your teams? Try AntsRoute free for 7 days, no commitment, and discover how it can adapt to your business and simplify last-mile logistics planning.
WRITTEN BY
Florine Martin
Florine has been a freelance web copywriter since 2021, writing for a variety of clients in a range of sectors. Since the beginning of 2024, she has been writing articles about logistics for our company, AntsRoute.
Free 7-day trial | No credit card required
Contenu
- Understanding Delivery Tracking Schedules
- End-to-End Management
- A Strategic Challenge for Your Business
- A Data-Driven Process… Powered by the Right Tools
- The 5 Common Mistakes in Delivery Tracking Planning
- Mistake 1: Planning Without Real-Time Data
- Mistake 2: Failing to Centralize Visibility Across Teams
- Mistake 3: Ignoring External Disruptions
- Mistake 4: Failing to Track or Use Logistics KPIs
- Mistake 5: Not Adapting the Schedule to Activity Fluctuations
- Best Practices for Effective Delivery Tracking Planning in 2025
- 1. Equip Yourself with Connected Planning Software
- 2. Centralize Communication for Collaborative Management
- 3. Integrate Activity Forecasting into Your Planning
- 4. Manage Your Performance with the Right KPIs
- 5. Automate to Save Time and Boost Efficiency