How artificial intelligence is helping companies to optimise their logistics processes
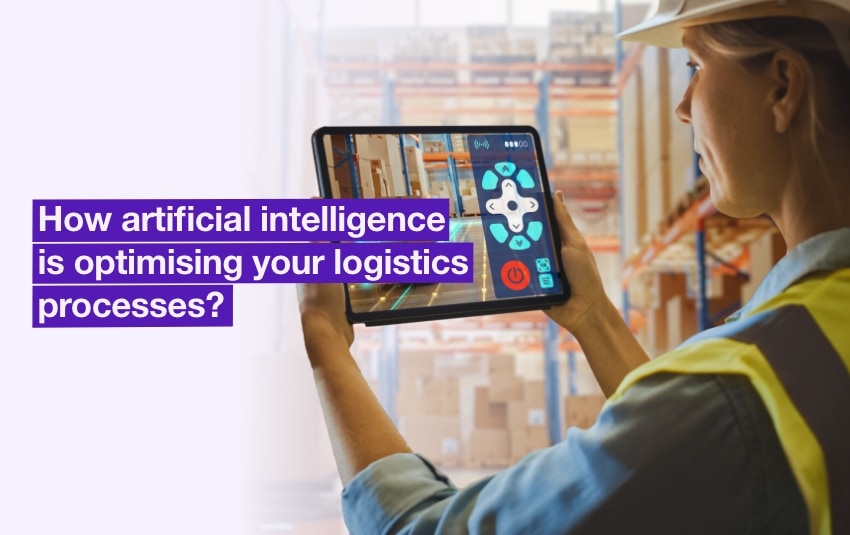
In a very tense global environment, supply chain managers are facing ever-greater challenges: shortages of labour and raw materials, high transport costs, etc.
To build a more resilient supply chain, most decision-makers have chosen their side: technological innovation.
Table of contents
- Logistical or generative AI: but what kind of intelligence are we talking about?
- The most relevant artificial intelligence applications for the logistics sector
Artificial intelligence is transforming today’s logistics challenges into opportunities. For supply chain managers, technological innovation is the key to creating a more resilient supply chain.
As shown by the Descartes 2023 survey about transport management, 44% of managers favour the automation of operations, and the smart use of information appears to be essential for creating value.
Among the tools available to make the most of available resources, artificial intelligence ranks at the top. But between the buzz and the science-fiction scenarios, it’s not always easy to see clearly.
Our company, which has been using artificial intelligence to optimise routes for almost 10 years, takes a look at this technology and its most relevant uses in the logistics industry.
Logistical or generative artificial intelligence: but what kind of intelligence are we talking about?
In just a few months, generative artificial intelligence programmes such as ChatGPT, DALL-E, and Midjourney have already won over hundreds of millions of users worldwide.
All these AIs, which are able to reproduce a task or series of tasks previously carried out by humans, are said to be weak. According to the UNESCO definition, this means that they are “capable of performing certain precise tasks autonomously but without consciousness, within a framework defined by humans and following decisions taken by humans alone”.
For the moment, strong AI, endowed with reason and sensitivity and capable of solving problems independently, only exists in the imagination!
Yet the performance of these weak AIs is already very impressive. To better understand how they work and what you can expect from them, we can distinguish between two methods of automated learning: machine learning and deep learning.

Artificial intelligence is transforming logistics processes.
Machine learning
This method teaches a machine to produce a result based on structured or semi-structured data such as geographical coordinates, customer databases, information about a fleet of vehicles, etc.
In everyday life, many systems integrate a layer of machine learning, such as the recommendation algorithms used by e-commerce sites and streaming platforms.
With each click, the machine refines its knowledge of your tastes and buying habits to develop increasingly personalised offers.
Our route optimisation software is also based on machine learning, and is constantly being improved by two PhDs in operational research. Thanks to these machine learning algorithms, AntsRoute can optimise highly complex routes with ever greater accuracy, taking into account a considerable amount of data, without any human intervention.
Imagine that your drivers regularly have to wait for the same customer before they can deliver. After each delivery, the software learns from these mistakes and calculates an even more accurate unloading time.
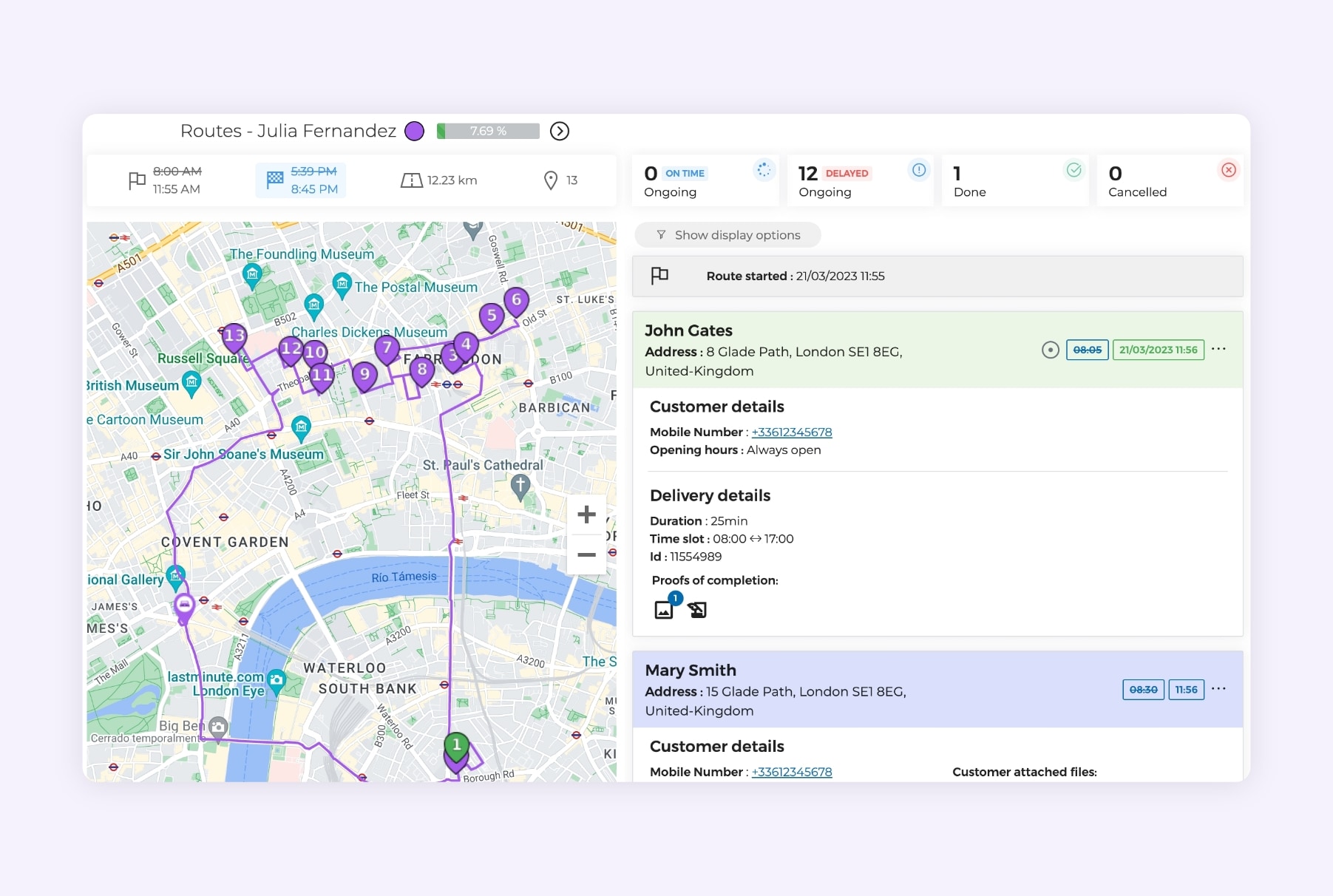
The AntsRoute route optimisation software is based on machine learning.
Deep learning
This technology is based on the use of neural networks, which are capable of establishing relationships between huge volumes of unstructured data in order to make decisions or predictions.
Thanks to deep learning, engineers have succeeded in developing such revolutionary solutions as automated translation software, image recognition software and autonomous robots that were unthinkable just a few years ago!
These systems, which go a long way towards imitating the human brain, nevertheless require computer resources and phenomenal amounts of data to be properly trained and produce satisfactory results.
The most relevant artificial intelligence applications for the logistics sector
Logistics very quickly emerged as an ideal field of application for artificial intelligence systems, with its vast data sets linked by well-studied cause-and-effect relationships.
Here is a summary of the most interesting use cases, from tools that are already operational to experiments that look very promising in the short term.
Predictive analysis of demand
One of the greatest challenges facing retail and distribution businesses is to adapt to customers’ demand in real time, without running the risk of stock-outs or unnecessary stockpiling.
This is particularly true of so-called weather-sensitive products, whose consumption varies according to climatic conditions: clothes, drinks, ice cream, heating or air-conditioning equipment, and so on.
A few degrees more or less, and purchases of these products soar or plummet, sometimes spectacularly.
As a result, professionals in these sectors have an interest in analysing their business history based on weather data from previous years to better anticipate buyer behaviour and adjust their orders.
Analysing demand according to the type of outlet is another very interesting use case for artificial intelligence, because the consumption of certain products varies greatly depending on the location of the shop, the social background of customers, and so on.
By cross-referencing all this data with the help of artificial intelligence, retail companies can optimise the management and supply of their different points of sale with great accuracy.
This information is also very useful for negotiating transport prices according to the urgency of orders.
Smart management of stocks
But for goods to reach shops or online merchants quickly, they need to be available in sufficient quantities upstream, in logistics warehouses located as close as possible to the end consumer.
Here again, cross-analysis of order history from previous years with data collected online or supplied by your customers is essential for optimum stock management.
Most warehouse management software (WMS) now integrates machine learning algorithms to support human decision-making by suggesting relevant product orders.
Some companies are going even further in their use of artificial intelligence by calling on digital twins, or device shadow. These are highly sophisticated simulation solutions that create a kind of digital mirror of your supply chain.
The aim of these systems is to simulate your supply chain in all its complexity and to calculate all possible scenarios and movements, in order to dynamically optimise the various flows of goods.
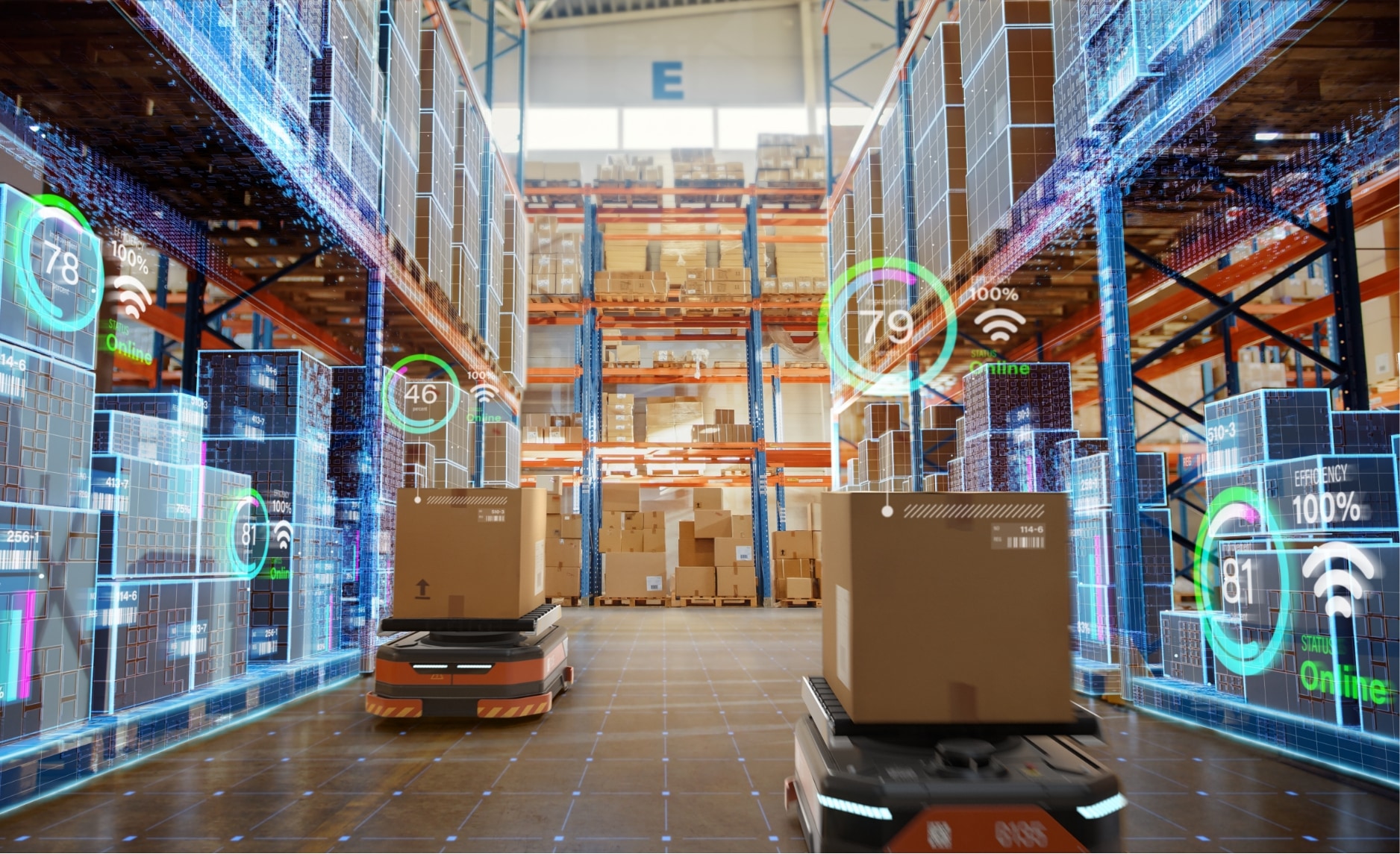
Robots and autonomous vehicles prepare orders.
Automated preparation of orders
Faced with a tight recruitment market, companies are finding it hard to attract and retain high-performing order pickers.
This is hardly surprising, given that these jobs, which are physically demanding and highly repetitive, are also often poorly paid.
More and more players in the logistics industry are therefore developing innovative solutions to improve working conditions for operators, and even to automate these jobs completely.
To reduce the number of movements made by operators within the warehouse, many stock management software systems, for example, determine the ideal location for each item based on parameters such as seasonality, turnover rate, type of item, etc.
There are also solutions that use artificial intelligence to automatically calculate the best picking route, so that each picker can efficiently collect all the references ordered without missing any.
To further optimise the costs of order preparation, the biggest players are also experimenting with autonomous robots and vehicles, i.e. those controlled by AI.
In a space that is normally very well organised, such as a warehouse, where traffic is reduced, these systems are already able to carry out complex tasks such as placing or picking up a parcel high up.
Some robots can even automatically pick up and drop off the product ordered, thanks to sensors connected to the packages.
Another application of AI that is booming is automated guided vehicles (AGVs). Able to move autonomously within warehouses, they can transport pallets of products through the shelves, to a loading bay, and so on.
Inventory by drone
Tedious and time-consuming, the inventory is nevertheless an essential task when it comes to rectifying the inevitable stock errors.
To automate this dreaded exercise, two companies from Grenoble, France, Hardis Group and Squadrone System, developed a drone called Eyesee in 2015.
In 2022, the start-up Darwin Drones took over Eyesee to industrialise its production and accelerate the commercial roll-out of the solution.
For this technology, which has long been the stuff of science fiction, is now mature and has already won over multinationals such as L’Oréal, Bayer and Ikea.
This drone can be flown manually or automatically, in indoor or outdoor storage areas. Thanks to an on-board camera connected to your warehouse management software, it can automatically recognise all kinds of barcodes, updating your stock data in record time.
This system, which uses computerised object identification, also detects the presence of pallets, racks or obstacles by analysing vertical lines and their breaks.
The progressive widespread use of these solutions should rapidly reduce costs and finally automate inventory with a very low error rate.
Delivery of goods by drones or autonomous vehicles
In the same vein, companies such as Amazon, Walmart and Kroger have experimented with delivery using autonomous mobile robots, either on the road or in the air.
For the moment, these technologies for transporting goods still involve too many risks of collision in an open area. Some goods are also too heavy or too fragile for such a mode of transport, not to mention the problem of protecting privacy.
However, the very fast progress being made in artificial intelligence should mean that these systems, which are less futuristic than they appear, will soon be in widespread use…
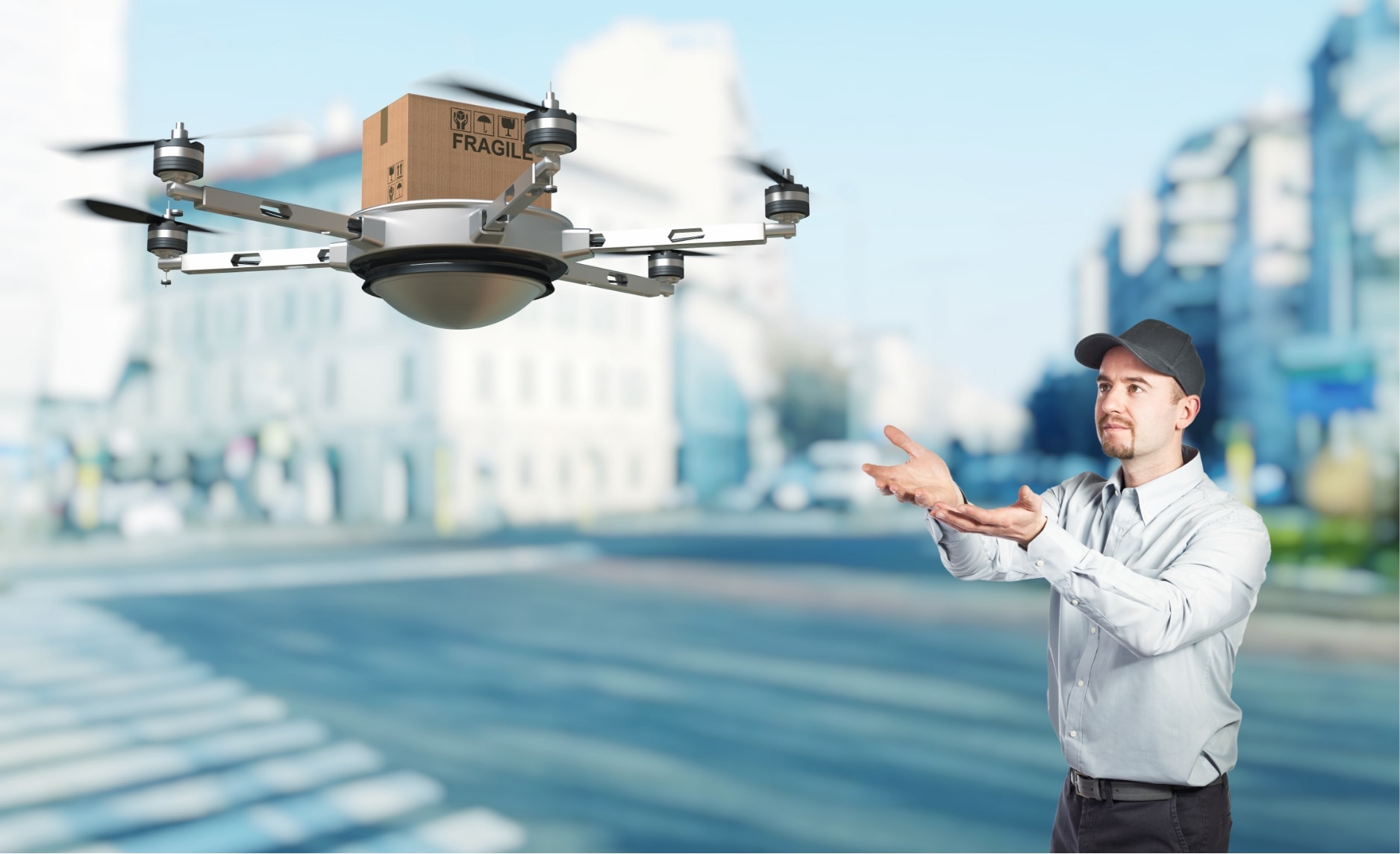
Some companies are experimenting with goods deliveries using drones.
Optimisation of transport routes
In the meantime, transporting goods in vehicles driven by human staff is still the biggest expense for logistics companies.
The last mile alone accounts for 20% of the real cost of a delivery, and this ratio can be as high as 50% in town centres.
To optimise the distances travelled, and therefore transport costs, our two PhDs in operational research have developed powerful algorithms based on combinatorial optimisation. This branch of mathematics is concerned with calculating the best solution from a finite but very large number of possibilities.
Thanks to these algorithms, combined with machine learning, our route management software is able to determine the best route for each delivery driver according to specific constraints.
Depending on your business, this may involve opening hours or the presence of the end customer, the level of service subscribed to, certain characteristics of the goods, the skills of the drivers, and so on.
But if you’re delivering to just one hundred customers a day, with constraints varying from one customer to the next, optimising routes by hand or with a spreadsheet quickly becomes a headache.
Only a high-performance IT solution will enable you to optimise all your flows, while taking account of the considerable volume of data available.
To test our route management software for 7 days, simply sign up here. The trial is free, with no commitment, and you don’t even need to enter your credit card number!
Free 7-day trial | No credit card required
Contenu
- Logistical or generative artificial intelligence: but what kind of intelligence are we talking about?
- Machine learning
- Deep learning
- The most relevant artificial intelligence applications for the logistics sector
- Predictive analysis of demand
- Smart management of stocks
- Automated preparation of orders
- Inventory by drone
- Delivery of goods by drones or autonomous vehicles
- Optimisation of transport routes