Boost the Profitability of your Deliveries: 5 Tips to Maximise the Fill Rate of your Trucks
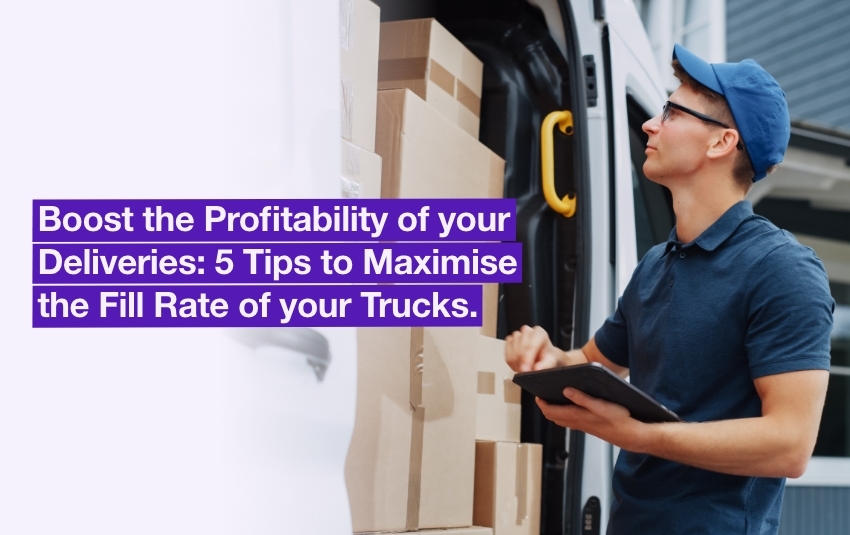
Transport is an essential pillar of the supply chain, linking the various stages from raw materials procurement to final delivery. It accounts for a significant part of transport costs and plays a crucial role in customer satisfaction, by guaranteeing reliable and on-time deliveries. However, poorly filled trucks lead to unnecessary expenditure, a high carbon footprint and overall inefficiency.
According to a study by the French Union of Transport and Logistics Companies (French: l’Union des entreprises Transport et Logistique de France), 20% of journeys in Europe are made empty in 2022.
Optimising truck fill rates is therefore a strategic lever for reducing logistics costs, improving profitability and minimising environmental impact.
This article explores best practices for maximising the efficiency of your deliveries while remaining competitive.
Table of contents:
- What is a truck’s fill rate?
- How to calculate the fill rate of a truck?
- What are the Challenges Involved in Optimising Truck Fill Rate?
- 5 Tips you Can Implement to Improve your Truck Fill Rate
What is a Truck’s Fill Rate?
A truck’s fill rate measures the use of its capacity, expressed in volume or weight in relation to its maximum capacity. A well-filled truck transports goods efficiently, limiting unused space.
This parameter is crucial because it directly impacts several key aspects:
- Financial: Reduced costs per unit transported through better use of capacities.
- Operational: Reduced number of journeys required, streamlining the supply chain and improving overall efficiency.
- Environmental: Reduced CO2 emissions per tonne transported, contributing to more sustainable logistics practices.
For example, a half-empty truck multiplies trips, increases fuel and maintenance costs. In short, it reduces overall profitability. This is why optimising the fill rate of your trucks helps avoid these costly mistakes.
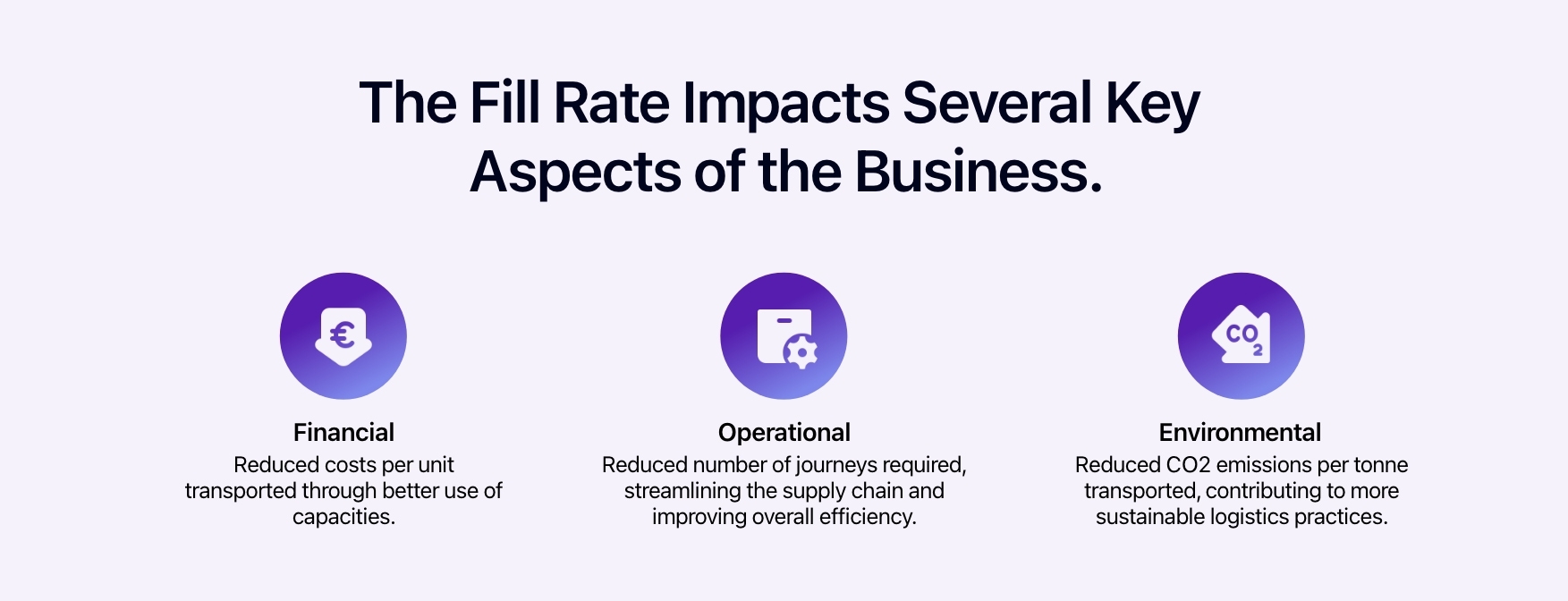
The aspects of the business that are affected by the truck fill rate.
How to Calculate the Fill Rate of a Truck?
Here’s how to calculate the fill rate of a truck and some things to consider to avoid common mistakes. The basic formula is as follows and allows you to evaluate in percentage how much of the volumetric space of the truck is used:
Fill Rate by Volume = (Volume Used / Total Volume Available) x 100
If you’re carrying heavy goods, you’ll want to calculate this rate by weight, as this constraint often limits the amount of space you can use. Here’s the formula to use:
Fill Rate by Weight = (Loaded Weight / Total Authorised Weight) x 100
To help you understand this calculation, we’ll give you a concrete example. A lorry capable of carrying 10 tonnes (10,000 kg) is loaded with goods weighing 8,000 kg.
Fill rate by weight = (8,000 / 10,000) x 100 = 80%.
In this case, 80% of the capacity by weight is used. In other words, the truck’s fill rate is 80%.
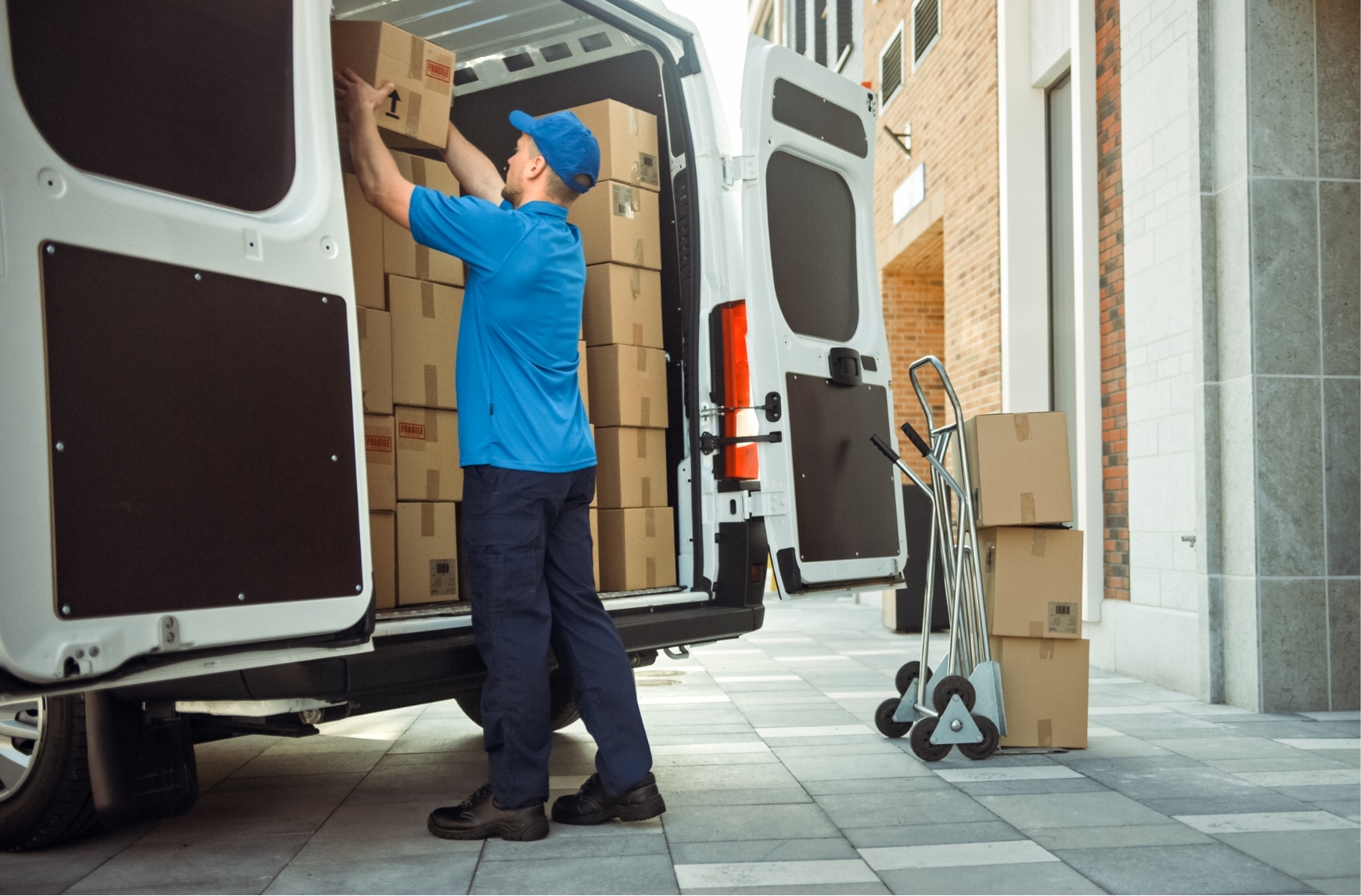
By calculating the fill rate, you can identify where there is room for improvement.
For a more realistic calculation of the fill rate, a few common mistakes should be avoided:
- Forget about unusable space: Some volumes in a truck (corners, empty spaces around goods) cannot be used efficiently.
- Overlooking the constraints related to goods:
- Fragile products requiring buffer spaces.
- Non-stackable goods reduce the use of space.
- Mixing metrics: Confusing volume and weight can distort results. For example, a lorry may be full by volume but underloaded by weight, or vice versa.
By calculating accurately and taking these three common mistakes into account, you’ll get a clear picture of the efficiency of your load and the scope for improvement.
What are the Challenges Involved in Optimising Truck Fill Rate?
Optimising truck fill rate can be complex due to various constraints and challenges specific to logistics. Here are the main issues to consider:
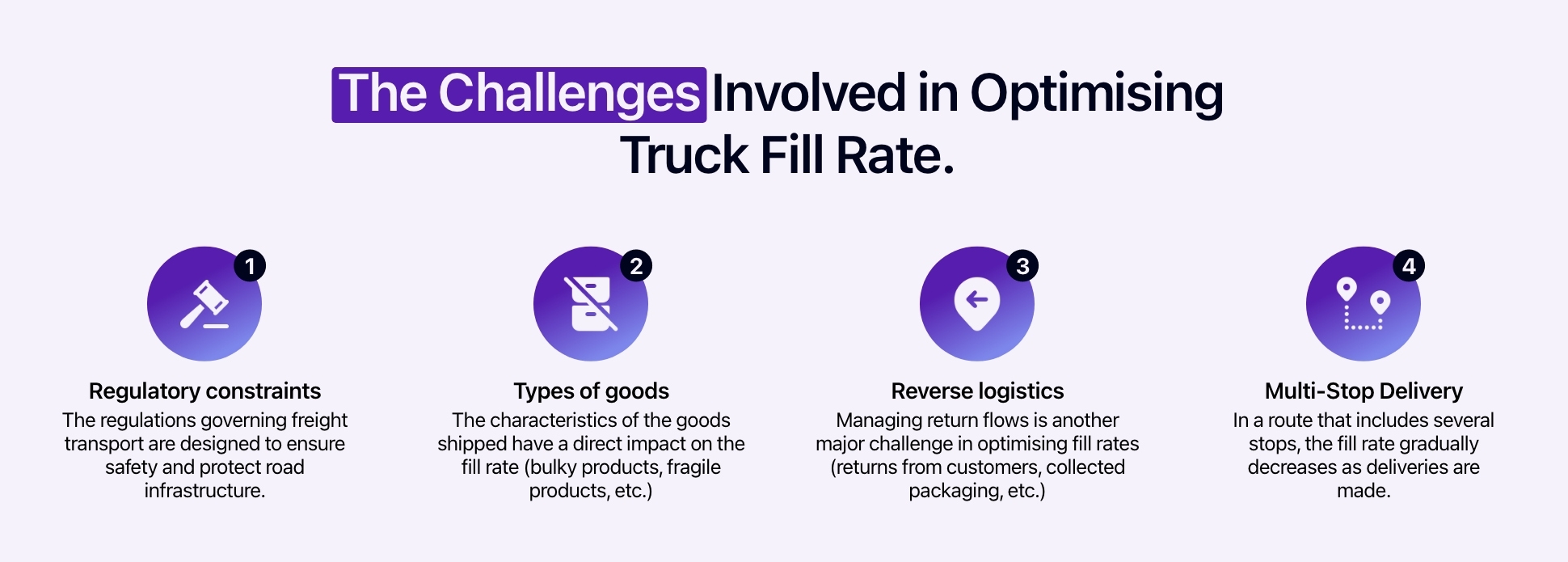
The 4 main challenges in optimising truck fill rate.
1. Regulatory constraints
The regulations governing freight transport are designed to ensure safety and protect road infrastructure. These constraints can limit the fill rate, in particular:
- Maximum authorised weight: Legislation imposes a total weight (truck + load) that must not be exceeded, which may restrict the actual capacity of the truck, even if the volumetric space is not fully used.
- Maximum dimensions: The dimensions of vehicles and their loads are also regulated, which can limit the possibilities for transporting bulky goods.
- Specific regulations: Certain goods, such as hazardous materials, require special authorisations and configurations, often reducing loading capacity..
2. Types of goods
The characteristics of the goods shipped have a direct impact on the fill rate:
- Bulky products: Items that take up a lot of space in relation to their weight, such as furniture or equipment, quickly occupy the space available, even if the weight capacity is far from being reached.
- Fragile products: These require buffer spaces to prevent shocks, reducing the use of space.
- Perishable products: Goods requiring refrigerated transport or special conditions (temperature, humidity) may require specific compartments, limiting the usable space.
- Non-stackable goods: Some products, such as fragile cardboard boxes, cannot be stacked on top of each other, resulting in under-utilisation of vertical space.
3. Reverse logistics
Managing return flows, or reverse logistics, is another major challenge in optimising fill rates:
- Returns from customers: Returns of damaged or non-compliant products must be taken into account in the loading plan, which can disorganise the initial layout.
- Collected packaging: Some routes involve collecting pallets, containers or other packaging, which takes up part of the truck’s space.
- Used or recyclable products: Transporting recyclable or end-of-life goods may require specific capacity, reducing that intended for the products delivered.
4. Multi-Stop Delivery
In a route that includes several stops, the fill rate gradually decreases as deliveries are made:
- Difficult planning: Optimisation must anticipate the needs of each delivery stop while maintaining efficient loading.
- Possible reorganisation: At each stop, the layout of the remaining goods can result in empty spaces that are difficult to reuse.
- Weight balancing: Progressive unloading can unbalance the truck, requiring an initial arrangement that does not make full use of the space.
The 4 constraints outlined above are all factors that complicate the optimisation of the fill rate. Identifying and anticipating these challenges is essential for developing effective and profitable logistics strategies.
5 Tips you Can Implement to Improve your Truck Fill Rate
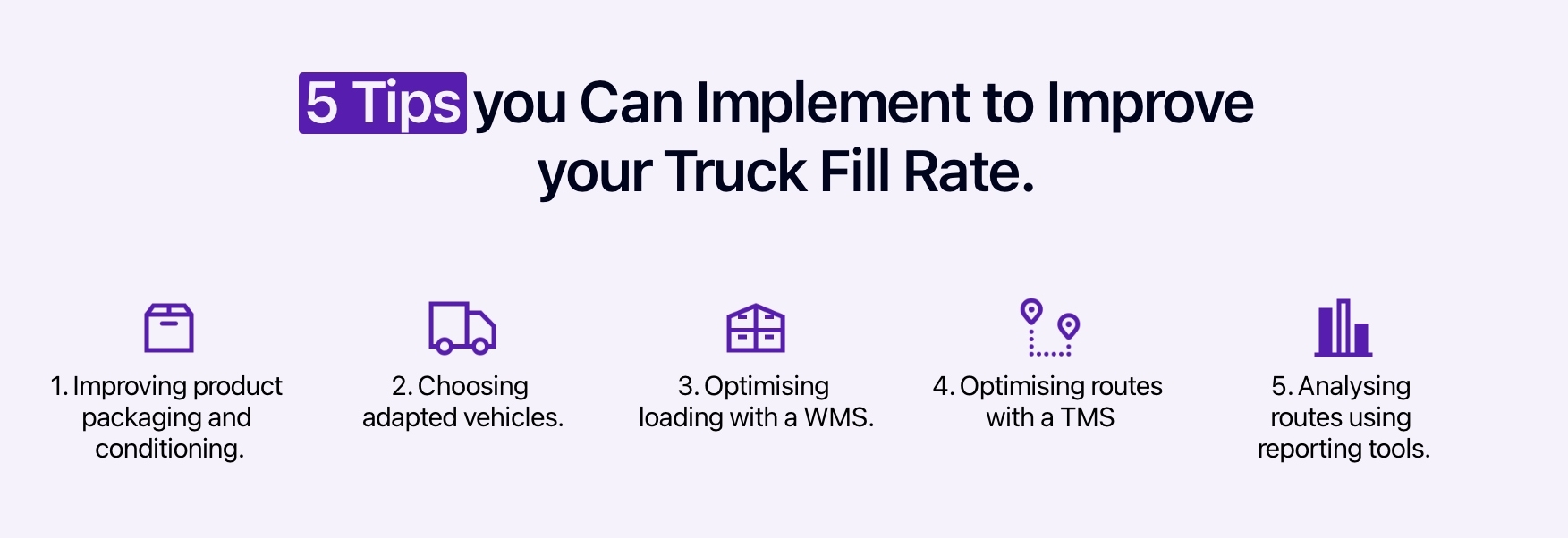
5 tips to improve the fill rate of trucks.
1. Improving product packaging and conditioning
Packaging plays a key role in optimising the truck fill rate. By adjusting packaging, it is possible to maximise the use of space while reducing costs. Here are the main actions to consider:
- Reduce the volume of packaging: To transport more goods in the same lorry, you can limit the space lost in secondary packaging and use customised packaging solutions adapted to the exact size of the products.
- Choose stackable, standardised shapes: Packaging with regular geometric shapes, such as rectangular or square boxes, makes loading easier and minimises empty space. What’s more, you can standardise the dimensions of your packaging to make stacking easier, whatever the type of product.
- Use lightweight materials: By choosing lighter materials, such as reinforced corrugated cardboard, you can reduce the overall weight of the load while maintaining the necessary strength.
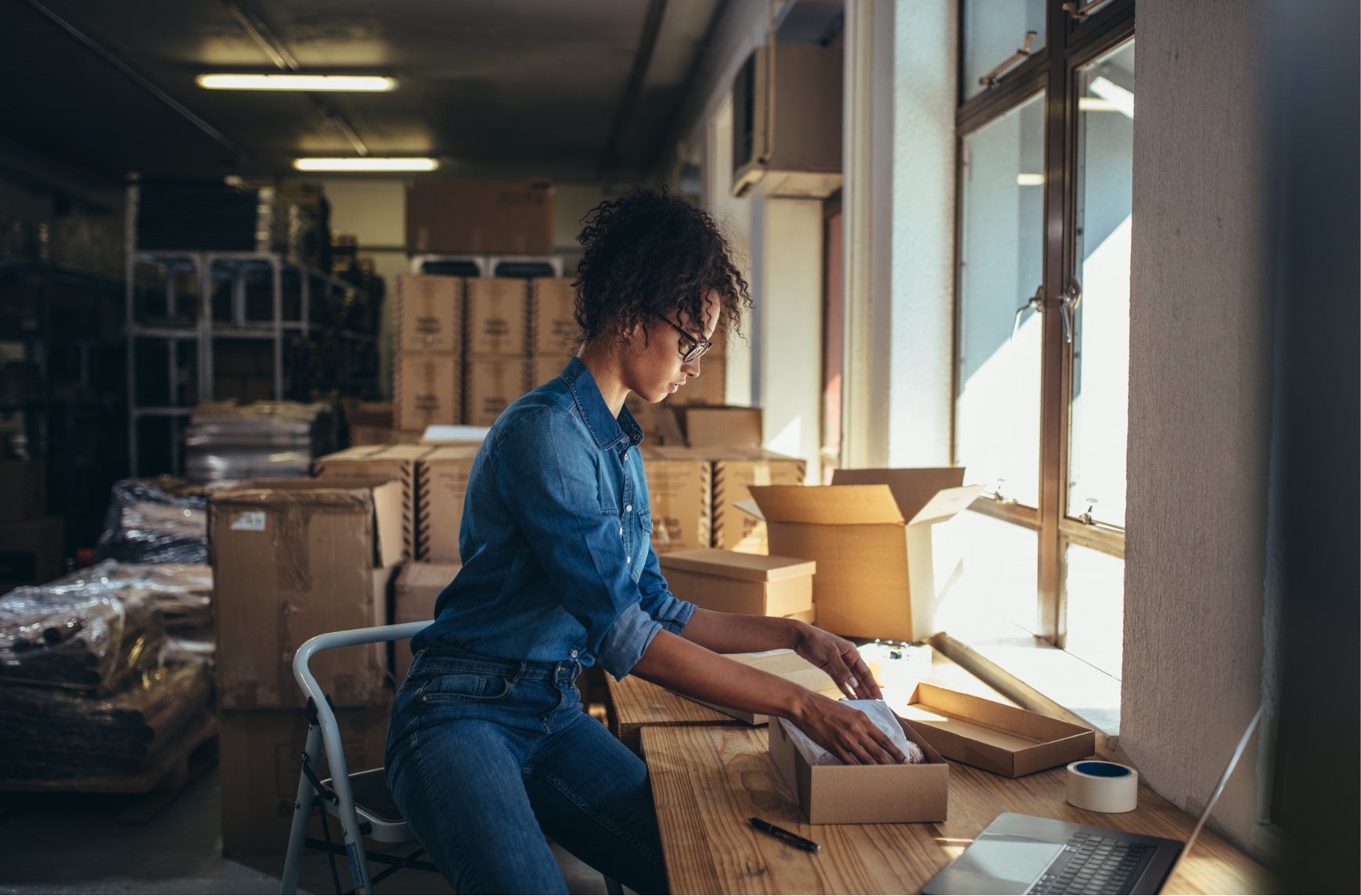
Optimising packaging increases the volume of products that can be transported.
Key points to remember: Well thought-out and optimised packaging has a dual advantage: it increases the volume of products that can be transported, while reducing the costs associated with extra journeys or unused space.
2. Choosing adapted vehicles
The choice of vehicle is a strategic decision when it comes to maximising the fill rate of trucks. By adapting the type of vehicle to the characteristics of the goods being transported, it is possible to make full use of the space available while optimising profitability. For example:
- Double deck trucks: These trucks have two loading levels, allowing more goods to be transported in the same volume. They are particularly useful for non-stackable or fragile products, as each level has a solid floor. The result: better use of vertical space and fewer journeys.
- Compartmented tankers: Designed for transporting liquids, these trucks are equipped with compartments that allow different types of liquid to be transported simultaneously without the risk of mixing. Each compartment is insulated, optimising safety and reducing the loss of unused space. Ideal for the food, chemical and oil industries.
Another solution: You can choose the size and type of vehicle according to the goods. For example:
- Small trucks or vans: Suitable for urban or low-volume deliveries, avoiding underfilling of larger trucks.
- Trucks with greater capacity: This type of vehicle is ideal for long journeys with considerable volumes.
- Dedicated vehicles: Particular configurations are required for certain types of goods (refrigerated, bulky, hazardous) to maximise the fill rate while complying with regulatory and safety constraints.
Key points to remember: Investing in vehicles that are adapted to the logistics needs of your business is a powerful lever for optimising the fill rate. Whether it’s exploiting vertical space with double deck trucks or rationalising liquid transport with compartmented tankers, the right choice of vehicle contributes directly to reducing costs and improving the overall efficiency of operations.
3. Optimising loading with a WMS (Warehouse Management System)
A WMS (Warehouse Management System) is an interesting tool for improving the fill rate of lorries. By optimising the management and layout of products in the warehouse, it maximises the use of available space while reducing errors.
First, this type of logistics tool enables precise planning of product layout. A WMS organises goods according to their dimensions, weight and delivery order. It calculates the best layout for loading the lorry efficiently, minimising empty spaces while respecting the constraints of the goods (fragility, accessibility). The planning also incorporates delivery priorities to avoid unnecessary unloading and reloading.
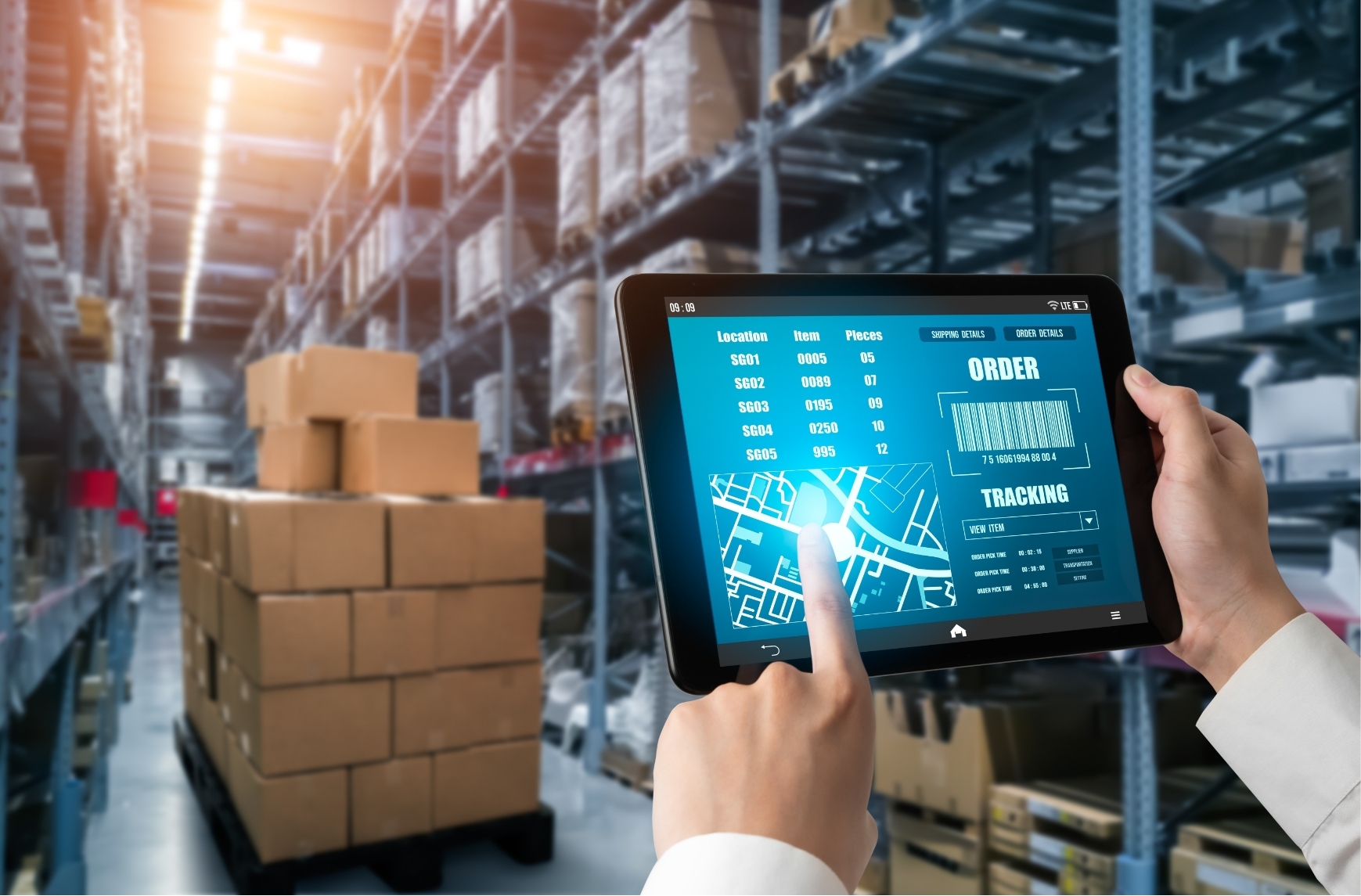
The use of a WMS enables smart management of lorry loading.
Another advantage of a warehouse management system is the 3D visualisation of loads to reduce wasted space. The 3D modelling functions can be used to simulate the loading of a truck before the operations have started. This helps to identify unused space and adjust the layout of products to maximise loading capacity. This visualisation also ensures optimal weight balancing, guaranteeing the vehicle’s stability.
Finally, the WMS automates processes to minimise human error. The tool automates loading management, reducing errors caused by approximate estimates or manual methods. It can generate clear instructions for operators or automated loading systems, ensuring accurate placement of goods. Thanks to this automation, your operations are faster and you avoid delays caused by last-minute adjustments.
Key points to remember: Thanks to the use of a WMS, you can intelligently and accurately manage the loading of your trucks, increasing their fill rate while improving the efficiency of your operations.
4. Optimising routes with a TMS (Transport Management System)
The optimisation of routes is a strategic lever for maximising truck fill rate and reducing logistics costs. Thanks to a TMS (Transport Management System) like AntsRoute, it is possible to significantly improve the efficiency of routes while minimising unnecessary journeys. Here are the three main advantages of these solutions:
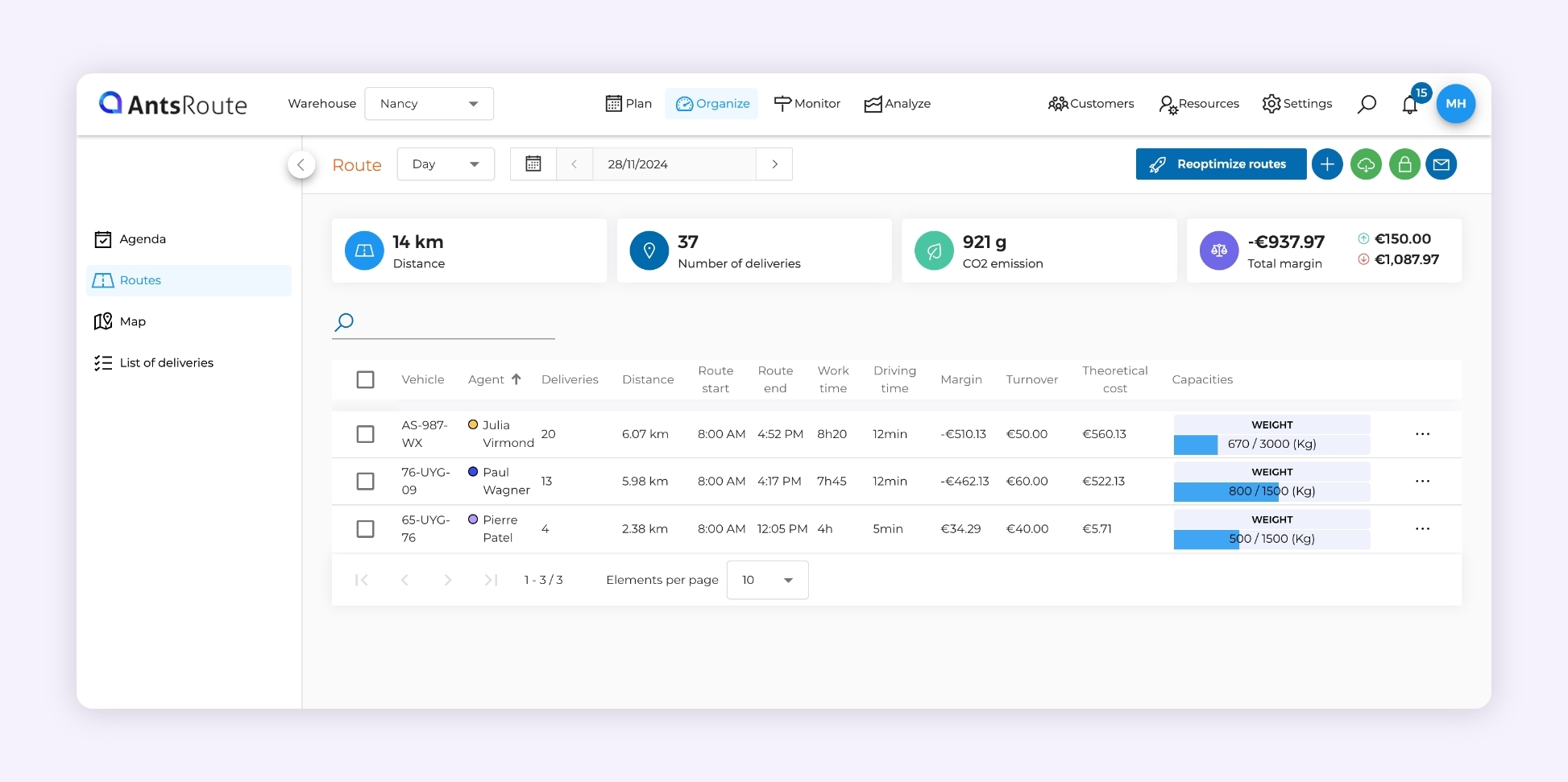
AntsRoute transport management software.
- Reducing unnecessary journeys: software like AntsRoute analyses routes according to criteria such as distance, traffic or delivery zones, in order to design the shortest and most efficient routes. By reducing the number of kilometres travelled, AntsRoute not only helps to save on fuel and maintenance costs, but also reduces CO2 emissions.
- Grouping orders to maximise the use of trucks: AntsRoute automatically groups orders whenever possible, based on their location and specific constraints (time slots required by customers, delivery time, type of goods). This allows trucks to be loaded to full capacity, limiting half-empty journeys and increasing the profitability per route.
Key points to remember: By using TMS software such as AntsRoute, companies can optimise their delivery routes and maximise truck fill rate, thereby reducing the costs associated with unnecessary journeys.
5. Analysing routes using reporting tools
The use of reporting tools is necessary to make your delivery routes ever more efficient and maximise the fill rate of your lorries. By exploiting reliable information, they offer the opportunity to identify gaps and adapt logistics strategies accordingly. Here are a few ideas.
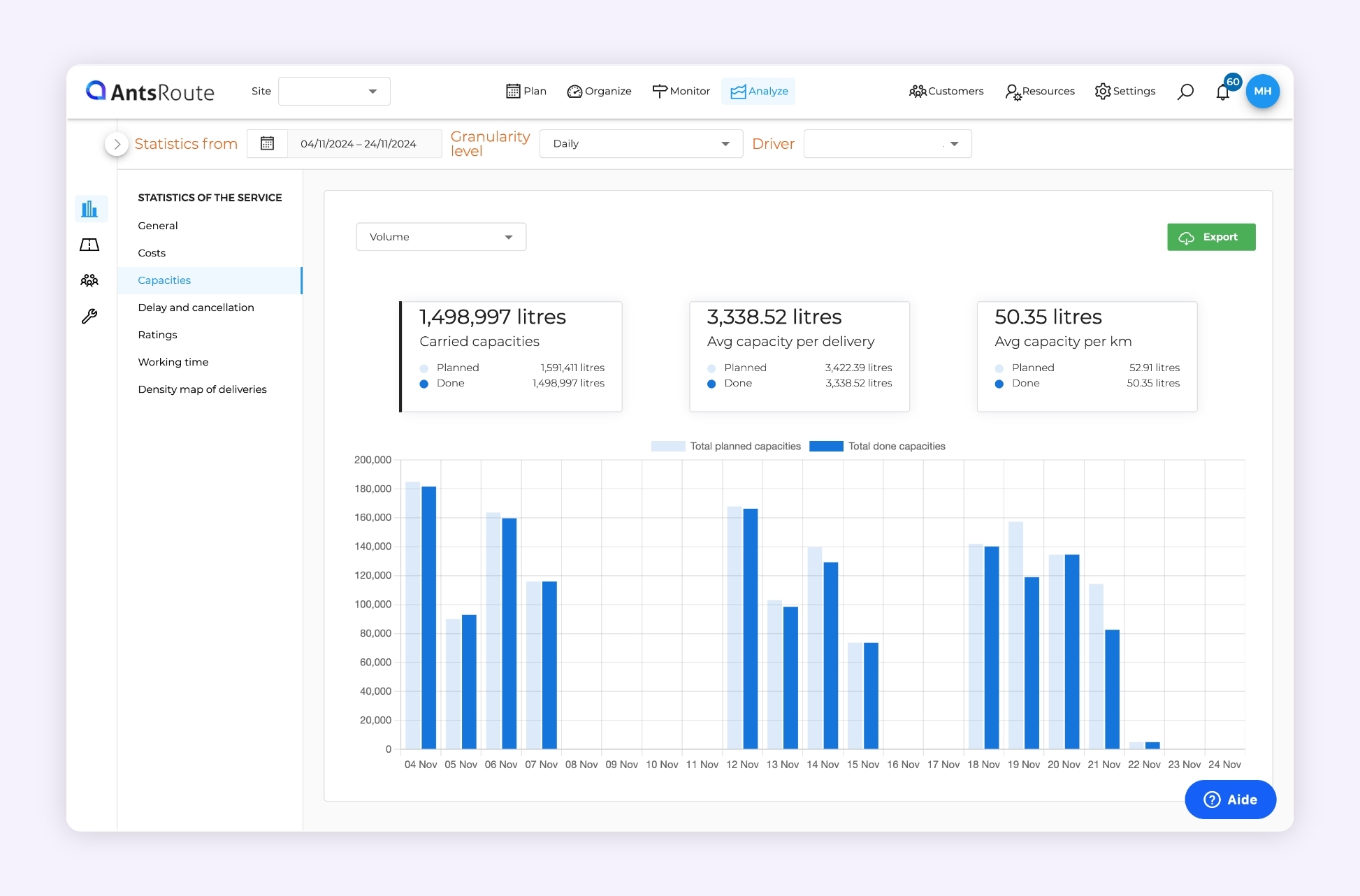
Analysis of logistics KPIs using AntsRoute software.
- Identification of under-used trucks: The detailed reports provide an overview of how trucks are being used. This makes it possible to quickly identify vehicles that are running half-empty or whose capacity is being poorly exploited. This analysis helps to optimise future routes by redistributing loads or adjusting the size of the vehicles used.
- Analysis of data to anticipate needs and adjust schedules: The data collected from past routes (number of deliveries, volumes and weights transported, types of goods) can be used to identify trends. This predictive analysis helps to anticipate logistics needs, such as seasonal volume increases. In this way, schedules can be adjusted to distribute goods more effectively and avoid unnecessary journeys.
- Implementation of KPIs (key indicators): Reporting tools can be used to monitor key logistics KPIs, such as the average fill rate (by volume and weight) or the cost per kilometre or per tonne transported. These indicators can be used to identify areas for improvement in logistics performance.
Key points to remember: Analysing routes with reporting tools helps to maximise fill rates. By identifying gaps, anticipating needs and monitoring relevant KPIs, companies can not only improve profitability, but also meet their sustainable and performance objectives..
Bonus: Technologies for better fill management
New technologies now offer powerful solutions for optimising truck fill rate. 3D simulation tools make it possible to create precise loading plans before departure. This maximises the use of available space. IoT sensors measure the weight and volume occupied in real time, ensuring dynamic management and avoiding errors. Finally, artificial intelligence and predictive algorithms analyse historical data and anticipate future orders to adjust loads and optimise routes. As well as optimising load factors, these innovations help to reduce costs, increase logistics efficiency and limit environmental impact.
Optimising truck fill rate offers considerable benefits: reduced costs, greater operational efficiency and a lower environmental footprint. By adopting high-performance tools such as AntsRoute’s route optimisation software, you can easily achieve these objectives. Plan efficient routes, maximise the use of your resources and boost your profitability. Test AntsRoute for free today and discover how you can turn your logistics into a real competitive advantage!
Free 7-day trial | No credit card required
Contenu
- What is a Truck’s Fill Rate?
- How to Calculate the Fill Rate of a Truck?
- What are the Challenges Involved in Optimising Truck Fill Rate?
- 1. Regulatory constraints
- 2. Types of goods
- 3. Reverse logistics
- 4. Multi-Stop Delivery
- 5 Tips you Can Implement to Improve your Truck Fill Rate
- 1. Improving product packaging and conditioning
- 2. Choosing adapted vehicles
- 3. Optimising loading with a WMS (Warehouse Management System)
- 4. Optimising routes with a TMS (Transport Management System)
- 5. Analysing routes using reporting tools
- Bonus: Technologies for better fill management