The solutions of the future to improve the management of field service operations
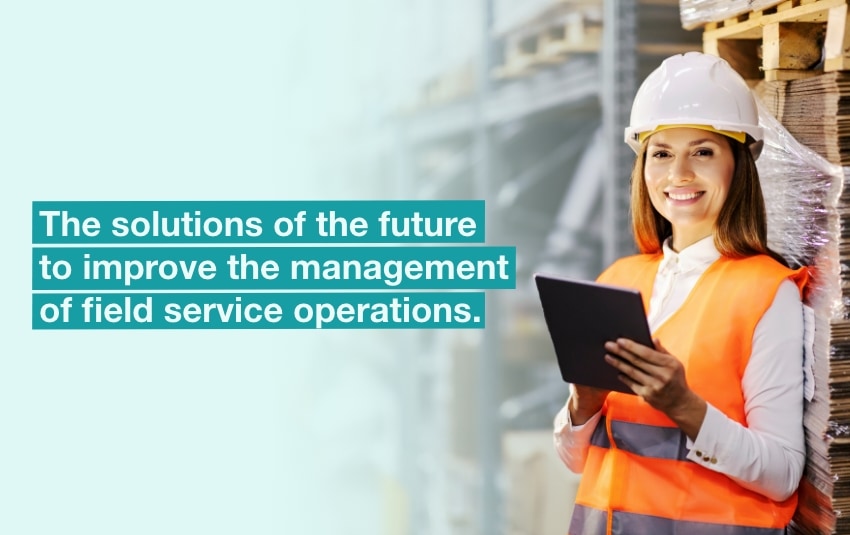
Blog > Field Service > The solutions of the future to improve the management of field service operations
The solutions of the future to improve the management of field service operations
Published on 2 March 2023 • Reading time: 6 min read
The cliché of the technician proudly helping out his customers, with his experience over his shoulder, is in a bad way.
To optimize the execution of field services, maintenance workers are increasingly connected to the company and its customers, as well as to multiple sources of information that are updated in real time.
Mobile apps, algorithms, automation, augmented reality, etc. Let’s take a look at the latest innovations in field service management!
Table of contents
- Field service management applications: an answer to the shortage of qualified technicians
- Increasingly sophisticated data management
- Other innovative solutions being deployed
Technologies are reinventing field service management. Innovative solutions are simplifying the day-to-day work of technicians, while improving their productivity. For service professionals, this means faster, more reliable operations.
Field service management applications: an answer to the shortage of qualified technicians
Today, the first difficulty for many companies is undoubtedly to guarantee the completion of the work orders already scheduled. Too often, hiring new qualified employees can be a real headache.
According to the latest survey by the Institute of the Motor Industry, the UK economy could see a shortfall of 2.6 million workers by 2030. The country could face a shortage of 25,000 qualified technicians.
Facilitate the integration of new employees with adapted tools
The companies explain this gap between supply and demand by the insufficient level of the graduates. Some managers also claim that their resilience and resistance to frustration are a little too fragile…
To facilitate the integration and limit the risk of demotivation, the field service management software and mobile applications offer very useful features.
In concrete terms, a tool such as AntsRoute helps field workers to go from one task to another thanks to an on-board navigation application.
This makes it easier to complete the field service routes, and the on-time rate of service for new employees increases more quickly.
Thanks to computerized maintenance management system (CMMS), each technician can also immediately find in the application all the relevant documents and resources online:
- References of spare parts or equipment to be loaded.
- History of visits and maintenance operations at the customer’s site.
- Building code, technical specifications, instructions for use, etc.
In this way, the mobile teams have all the information needed to succeed in their task from the very first visit.
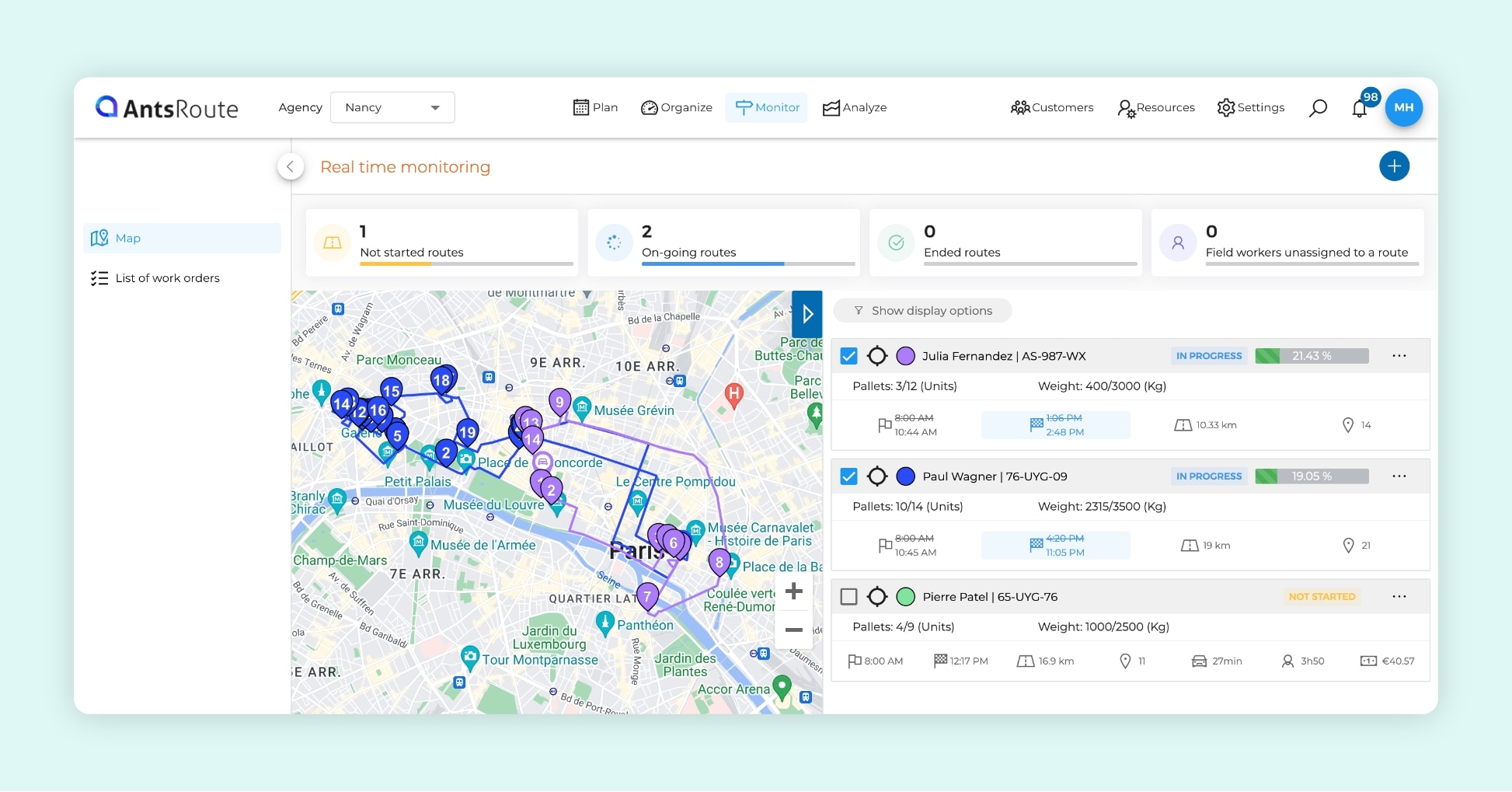
The AntsRoute route optimisation software.
Retain skilled workers by lightening their workload
The service management applications are also very useful for automating the writing of service reports, which is often considered as a burden by the teams in the field.
Today, it takes technicians less than 5 minutes to complete and send customised forms: fields to be filled in or boxes to be checked off, drop-down lists, etc. Not forgetting the proof of service with photos, which is very much appreciated by employees.
There are some field service management tools, such as AntsRoute, that even take into account individual preferences to automate the assignment of tasks:
- Favorite technician of the customer.
- Geographical sectorisation of field services.
- Home address if the technician starts the route from home, etc.
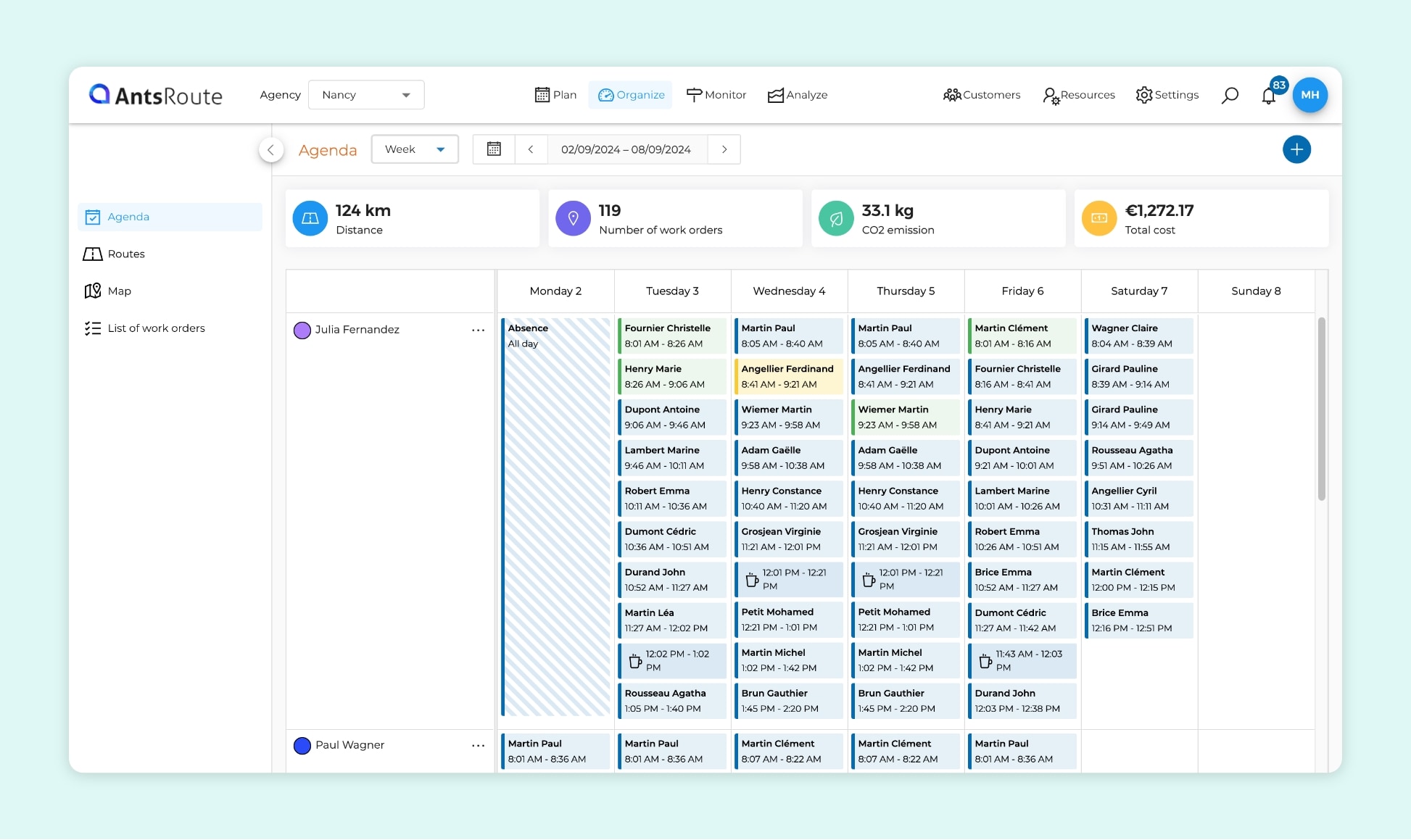
The optimisation of field service routes on AntsRoute.
Increasingly sophisticated data management
In the field service management (FSM) sector, companies can now choose from a wide range of software and applications, tailored to each type of activity.
Interconnecting IT solutions, an affordable method for everyone
To achieve a precise objective, specialised software will always be more effective than an all-in-one solution… like the tools your technicians use on a daily basis.
Based on this principle, more and more companies are combining several different but interconnected IT solutions:
- CMMS tool to monitor and manage stocks of equipment, spare parts, consumables, etc.
- Route optimisation software to smartly assign the tasks and save vehicle and fuel costs.
- Customer Relationship Management (CRM) solution.
- Dedicated application to collect payments directly from the field.
- Human resources software, etc.
To interconnect these different tools, there is no longer any need for an in-house IT department, or even knowledge of coding. Every company can now have access to them, including the smallest!
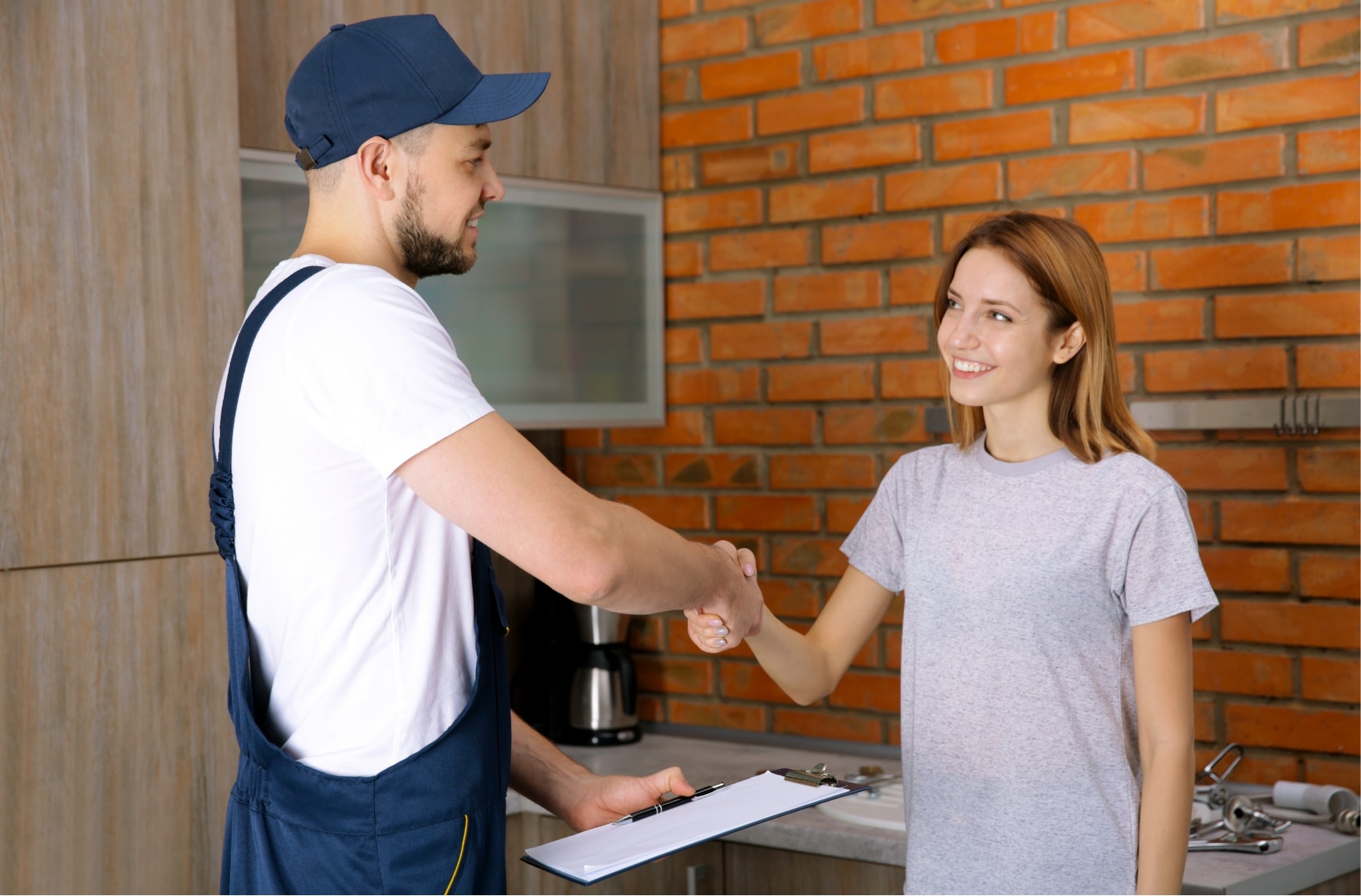
Software improves the management of field operations.
Analyse geographical data in real time
An increasing number of solutions also include geolocation functionalities, in very different ways.
Some maintenance software, for example, cross-references facility or equipment plans with data provided by a Geographic Information System (GIS). This is a very valuable method for quickly locating a valve or a leak in an industrial pipe in the field!
In another way, route planning software uses impressive sets of instructions, called algorithms, to optimise the routes of each team member. To achieve this, a tool like AntsRoute takes into account and analyses thousands of pieces of data:
- Skills and authorisations of each technician.
- Time slots desired by customers.
- Location and availability of equipment and spare parts.
- Characteristics and fuel consumption of vehicles, etc.
These very powerful algorithms, sometimes wrongly called artificial intelligence, also help managers to make the best decisions in real time.
In the event of an unforeseen event or crash, software such as AntsRoute calculates and compares all possible scenarios, for example, based on the precise geographical location of each available technician.
As soon as the team leader has validated the alternative option, the technicians and the customer are notified in real time by e-mail or SMS. It ensures an automated end-to-end communication.
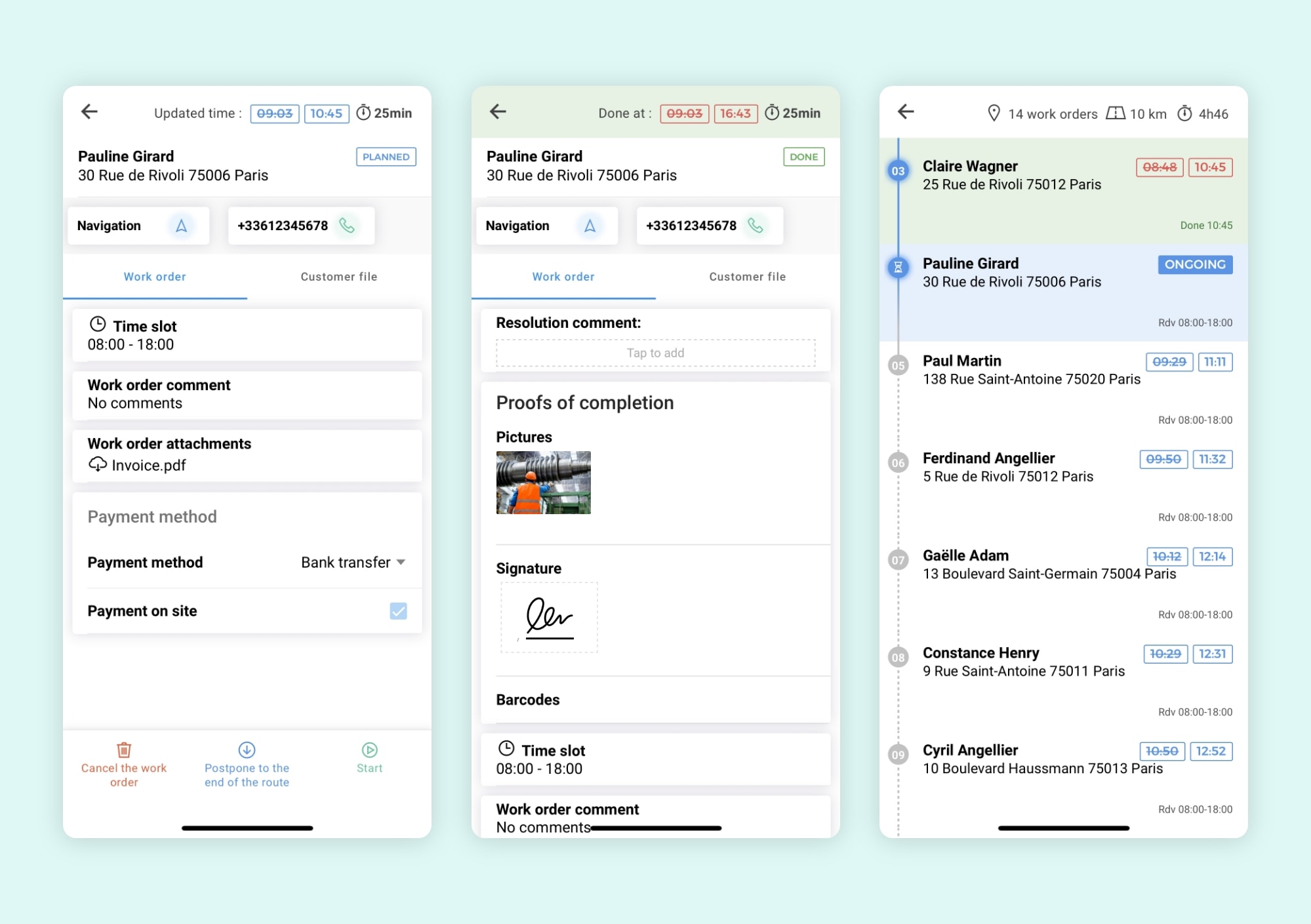
The AntsRoute mobile application makes life easier for mobile technicians.
Other innovative solutions being deployed
To support the activities of service companies in the field, even more innovative solutions are being implemented.
For example, predictive maintenance professionals have hopes for systems of connected objects equipped with sensors, which are capable of transmitting very precise data on their operating status in real time.
These new technologies based on the Internet of Things (IoT) should enable professionals to track and monitor the condition of equipment remotely, thus promoting continuous predictive maintenance.
There are also companies which use drones and robots to inspect dangerous or hard-to-reach facilities:
- Road structure ;
- Wind turbines ;
- Electrical networks, etc.
Used in combination with machine learning (ML) systems, these technologies are proving to be very effective in reducing the cost of maintaining remote equipment, while at the same time limiting work-related accidents.
In the same vein, the use of augmented reality glasses or headsets should not surprise people anymore.
The augmented reality will somehow be added to the real environment of the technician to guide him in the completion of his tasks, by providing him at any time with the most relevant information stored in the cloud.
Would you like to discover AntsRoute to plan your field services and optimise your team’s routes? Register for free here to test the software in real conditions and quickly improve your management processes!
Free 7-day trial | No credit card required
Contenu
- Field service management applications: an answer to the shortage of qualified technicians
- Facilitate the integration of new employees with adapted tools
- Retain skilled workers by lightening their workload
- Increasingly sophisticated data management
- Interconnecting IT solutions, an affordable method for everyone
- Analyse geographical data in real time
- Other innovative solutions being deployed