Create a maintenance schedule: the complete guide
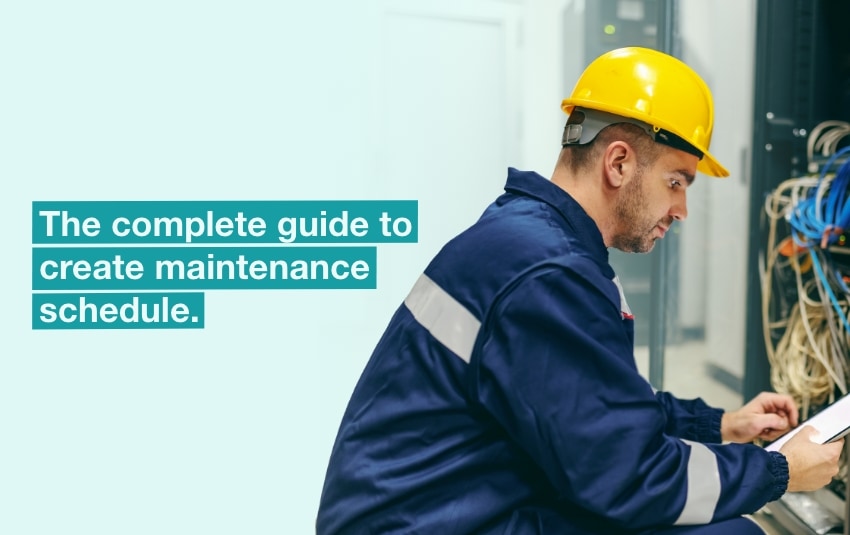
Blog > Field Service > Create a maintenance schedule: the complete guide
Create a maintenance schedule: the complete guide
Published on 26 June 2023 • Reading time: 8 min read
Creating and managing the maintenance schedule is an essential task for any manager in charge of a team of technicians.
Such a tool is essential for companies whose core business is maintenance, as well as for industries that have their own fleet of machines and equipment.
To help you build an effective and realistic maintenance schedule, our guide takes you through each step:
- Definition of maintenance schedule
- Information and data to be gathered
- The difference between the maintenance plan and the maintenance schedule
- The main steps to follow to create an effective schedule
- Which IT tool should you use to manage your maintenance schedule?
- 5 good reasons to create a maintenance schedule
Creating an effective and workable maintenance schedule is essential. CMMS and route optimisation software simplify the planning of maintenance operations. These tools enable better management of fields technicians and make it easier to deal with emergencies.
What is maintenance schedule?
A maintenance schedule is a document that clearly defines the distribution of maintenance tasks for a given period and team.
It usually takes the form of a calendar or spreadsheet.
In practical terms, a maintenance schedule means that each job can be assigned to a technician within a satisfactory timeframe, taking into account the skills, authorisations, and licences of each field worker.
Depending on your needs and the way your company is organised, the planning can be daily, weekly or monthly.
The right schedule includes all the types of maintenance to be carried out, prioritising them according to their degree of emergency:
- Systematic preventive maintenance. For example, greasing the bearings on a motor every month or every year.
- Conditional preventive maintenance, when a piece of equipment exceeds a predefined threshold. For example, replenishing the oil level of a hydraulic unit if it has dropped too low.
- Predictive maintenance, when a set of parameters suggests that a breakdown or deterioration is imminent.
- Palliative maintenance, to bring a piece of equipment back into service, at least temporarily. In everyday language, this is referred to as “troubleshooting”.
- Corrective maintenance, when a technician replaces defective equipment with new equipment to ensure a lasting repair.
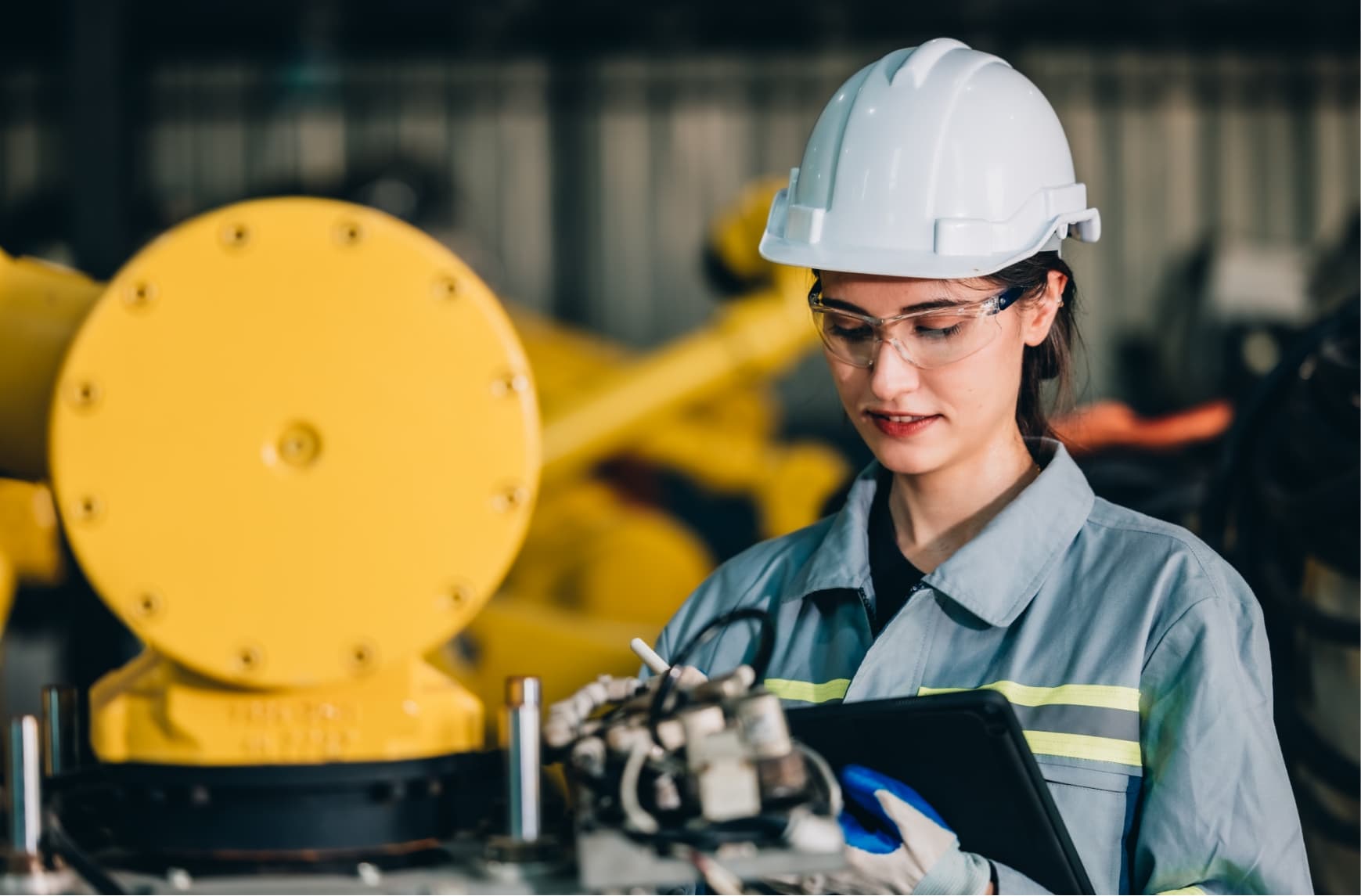
The maintenance schedule is used to assign each work order to a technician.
Information and data to be gathered
A useful and effective maintenance schedule includes a list of precise information about the operations to be carried out:
- Equipment or material concerned.
- Name of the technicians assigned to the operation.
- Nature and purpose of the operation: check-up, monthly maintenance, part to be replaced, etc.
- Spare parts, equipment, and tools to be prepared.
- Level of priority: planned, urgent or critical work.
- Duration on site, based for example on the data provided by the manufacturer.
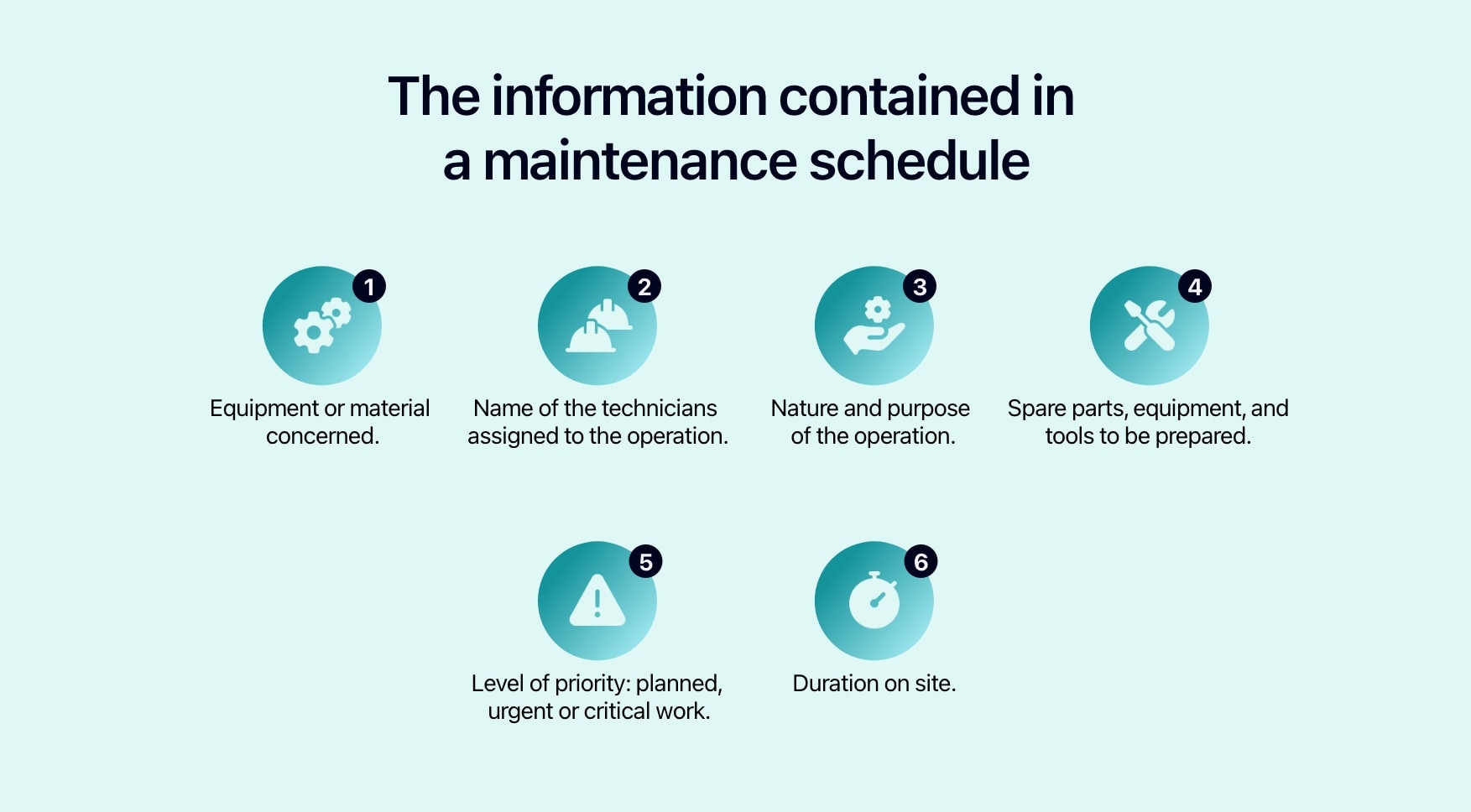
The information contained in the maintenance schedule.
Of course, this list can be adapted to suit your needs. Depending on your business sector and the way your team operates, other data may be relevant:
- Name of contact person and exact address if the technician is going to a customer site or an off-site location.
- Type or number plate of the vehicle to be used.
- Details of the shop or warehouse where the spare part can be collected, etc.
What is the difference between a maintenance plan and a maintenance schedule?
According to standard NF EN 13306, the maintenance plan can be defined as “structured and documented set of tasks that includes the activities, work instructions, resources, and time required to carry out the maintenance”.
The maintenance plan therefore includes a whole series of documents and procedures designed to keep or restore equipment in good working condition. It takes into account:
- The frequency and nature of maintenance operations recommended by the manufacturer.
- The contractual commitments made by your company to its customers.
- The laws and regulations in force in the countries where your teams operate.
To create an efficient schedule, you will need some of the information listed in the maintenance plan. But the two documents have neither the same function nor the same purpose.
In simple terms, the maintenance schedule sets out and organises in both space and time all the operations recommended in the maintenance plan, based on the human and material resources available.
The main steps to follow to create a workable maintenance schedule
1. Plan preventive maintenance operations
Let’s take the example of a heating company that provides annual maintenance contracts tailored to each type of boiler. Initially, you’ll need to plan all these recurring visits, which are essential to meet your contractual commitments.
By doing this, you can optimise the schedules of your teams for each period, without being delayed by their holidays or those of customers.
2. Keep a safety margin for the unexpected events
Depending on your activity, you’ll need to leave enough leeway for emergencies and unforeseen circumstances.
The heating company in this example is also in demand during the summer months for repairs to air conditioning units.
It will also need to keep slots free to respond quickly to requests from new customers.
3. Plan emergency repairs and unforeseen incidents
By doing this, you can respond to unscheduled requests with more confidence and assign them to one or other of your technicians according to various parameters:
- Distance to be driven to reach the site.
- Skills required.
- Occupancy rate of team members, etc.
4. Analyse the results to optimise your performance
Finally, you need to analyse your key performance indicators (KPIs) at regular frequencies to plan future operations smarter.
Let’s say that the boiler takes much longer to repair because of an atypical configuration.
Based on your actual statistics, you can adjust the forecast duration of future operations, and thus create more realistic schedules.
Which IT tool should you use to manage your maintenance schedule?
Excel, the first choice
Many companies start planning service routes using software such as Excel or its online alternative, Google Sheets.
These solutions, which are very simple to set up, can indeed be useful for managing a limited number of technicians and operations.
However, they have some limitations that are frustrating to use, even for a small team.
For example, you will have to send your technicians the documents and attachments they need to carry out their tasks separately.
Your employees will also have to use a navigation app, and you won’t be able to geolocate them or track their work in real time.
There are also companies that manage small technical teams using a shared calendar solution. Among the most popular are Google Calendar and Microsoft Outlook.
Synchronised in real time, these online calendars by definition work with the other tools in the IT package chosen by your company (Google Workspace, Microsoft 365, etc.). They make it easy to associate notes or plans with each appointment.
However, they are not designed to be used as a management tool. This means that you’ll need to be constantly thinking about solutions for linking up with your spare parts stock, writing quotations or invoices, extracting performance indicators, etc.
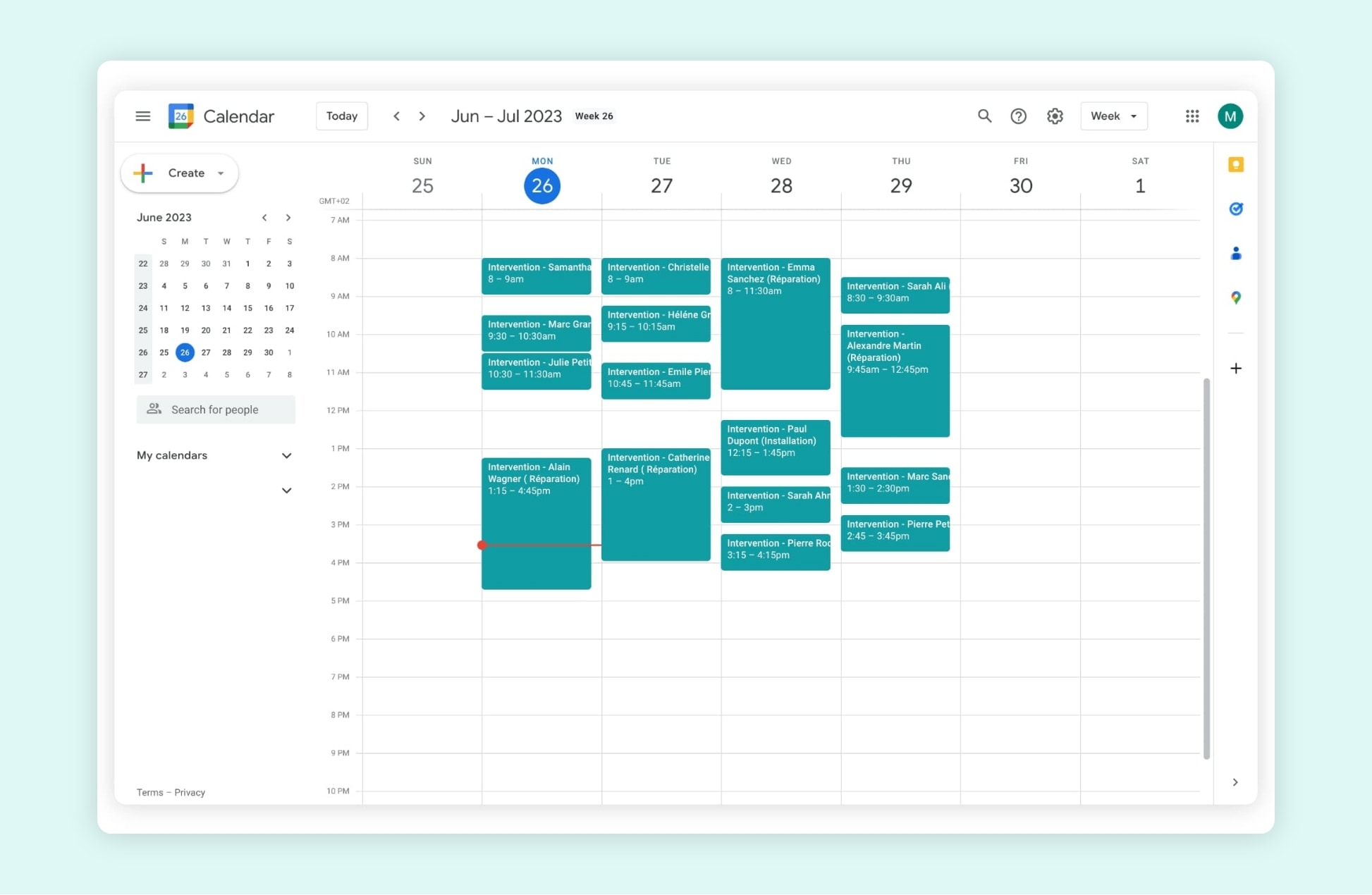
The Google shared calendar.
Maintenance management software
Most Computerised Maintenance Management Systems (CMMS) offer some very interesting features to help you organise the work of your teams more effectively, such as:
- Equipment and spare parts stock management.
- Help with planning preventive maintenance operations.
- Step-by-step monitoring of operations.
- History of checks and repairs carried out on the customer’s premises.
- Performance indicators, etc.
Some CMMS solutions even include mapping and communication tools, making them almost like field service operation management software.
Before adopting such software, you should take an in-depth look at the services it can provide. What are the different ways of scheduling and making appointments? Does the tool include a real-time navigation or geolocation solution for technicians?
You also need to take into account the time it takes to get to know the software, as some of it is not very intuitive, and check the real cost of using it, all options included.
Route optimisation software
As their name suggests, these tools are extremely useful for optimising the work of mobile service teams.
They can be used on their own or in addition to spreadsheets, CMMS software, etc.
Not only does this optimisation software save you a significant amount of time on the planning itself, it also systematically determines the best route for each technician based on various parameters:
- Maximum time to visit the customer site.
- Level of priority of the operation (preventive maintenance, urgent repairs, etc.).
- Geographical location of the operation.
- Skills or authorisations required.
- HR constraints (working hours, holidays, unforeseen absences, etc.).
- Information on the road network, such as recurring traffic jams, etc.
The icing on the cake: some field service management tools, such as AntsRoute, can also track the progress of technicians and automate the communication with customers in real time.
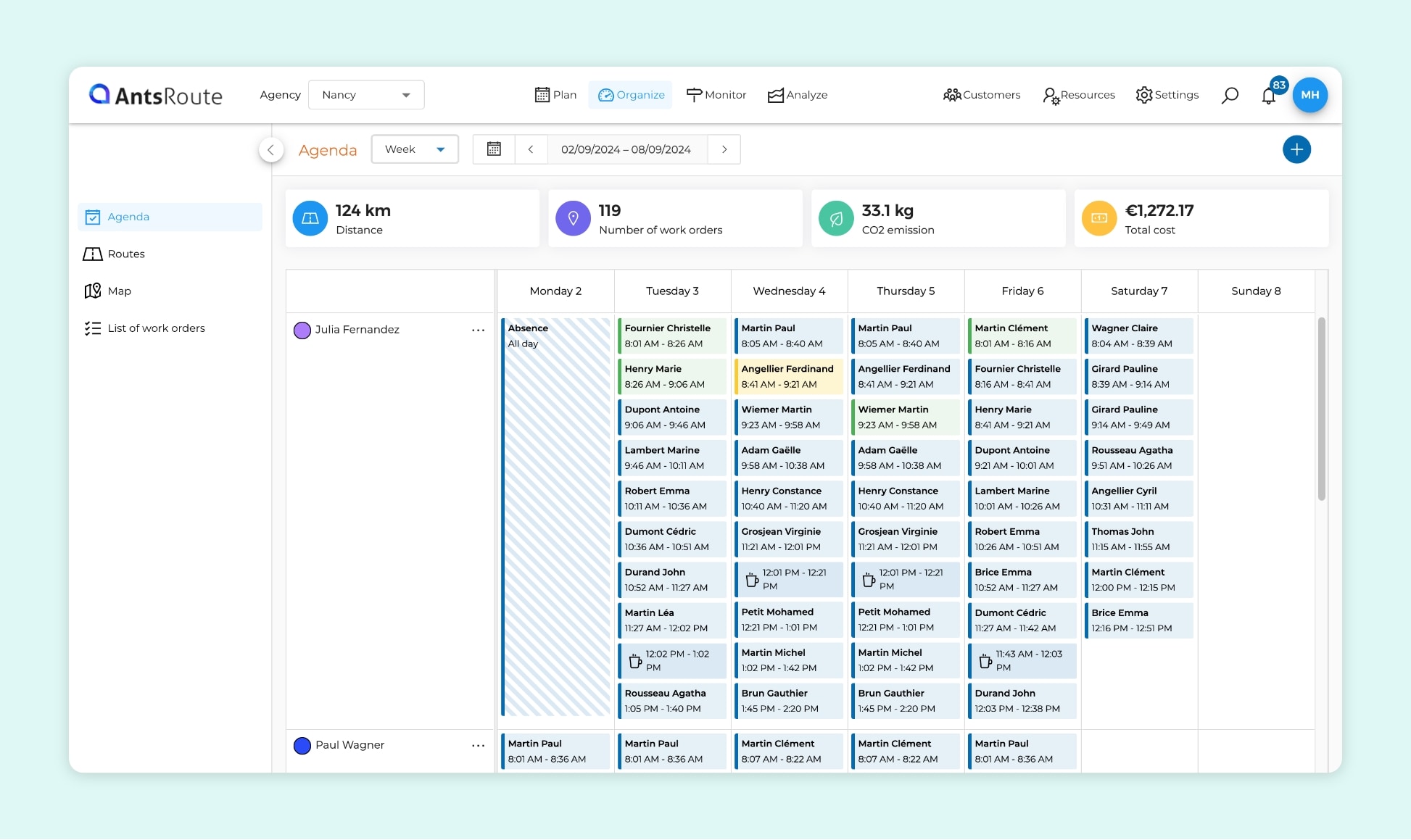
View of a weekly maintenance schedule on AntsRoute.
5 good reasons to create your maintenance schedule
These 5 arguments should convince you of the benefits and added value of this tool.
You can allocate company resources smarter
In a highly constrained environment, this type of planning enables you to share out the workload more effectively, and therefore optimise the resources available.
Do you need to send one of your technicians to a very remote site to resolve an urgent breakdown? Thanks to a well-organised work schedule, you can assign other preventive maintenance operations to this technician in just a few clicks, and thus cancel the inspection visit scheduled shortly afterwards.
You can manage emergencies and unforeseen events more easily
In this type of business, managing major or even critical breakdowns is part of everyday life. But managers need to have the right tools in hand to respond quickly to these requests without overlooking service quality.
Thanks to functions such as geolocation and real-time validation of operations, the software locates the best technician in the area and notifies him or her immediately.
You can improve your profitability
The rigorous planning of preventive maintenance extends the life of your equipment and avoids the penalties associated with non-compliance with your commitments.
By optimising preventive and corrective maintenance tasks, you can also increase the number of tasks carried out per day and per technician, generating significant savings on vehicle and fuel costs.
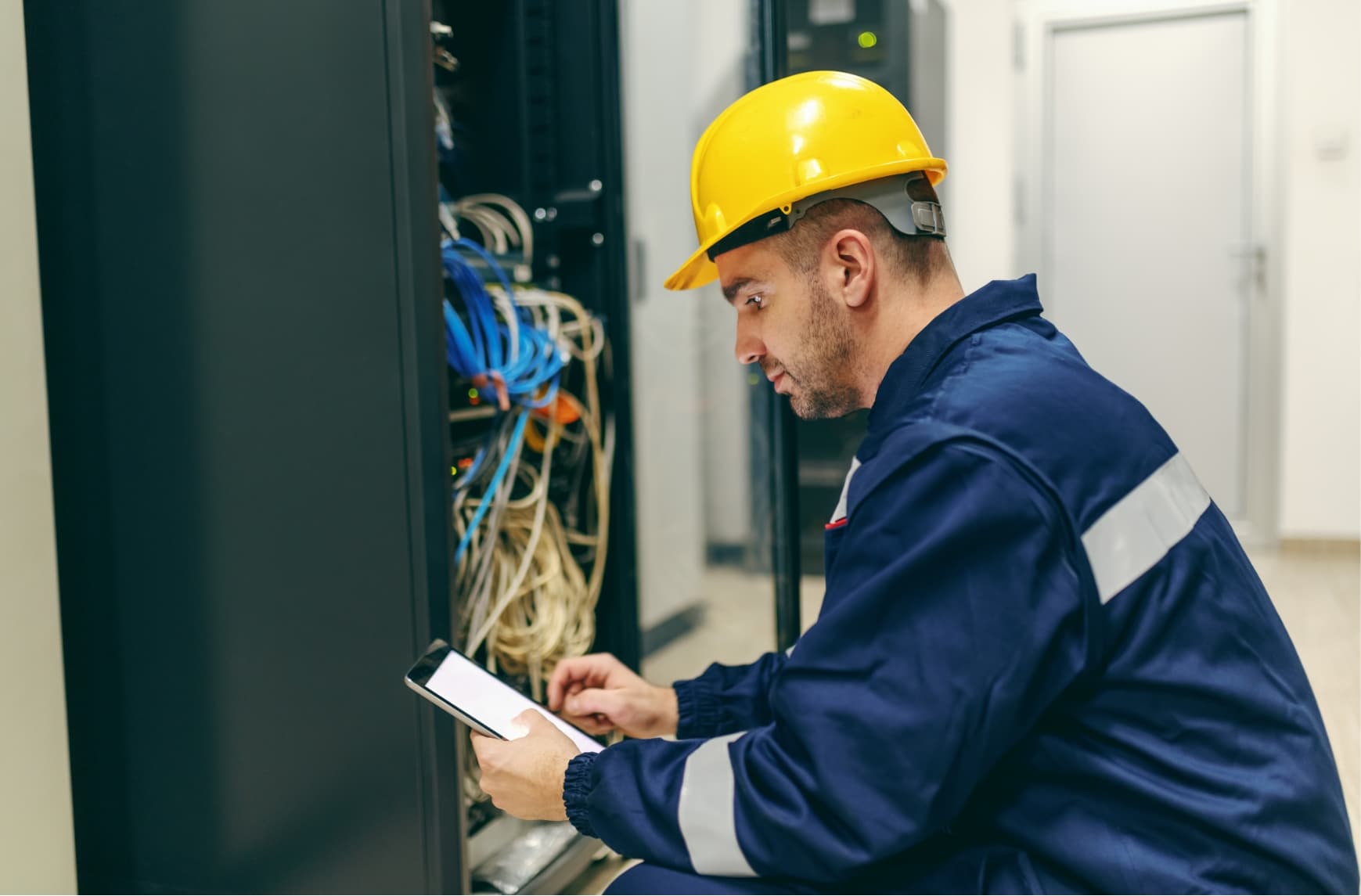
The optimisation of maintenance schedules enables more work to be carried out.
You increase the loyalty of your current technicians
The regular maintenance of equipment limits the number of incidents and shutdowns, which are always very stressful for employees.
After all, how can you stay motivated when your machines are regularly down and the simplest spare part change turns into an obstacle course?
If your company works on behalf of external customers, an efficient and well-maintained maintenance schedule is also very useful for retaining your technicians. In fact, very few of them enjoy writing service reports or making repeated calls to cancel or reschedule appointments.
Freed from this time-consuming and unrewarding part of the job, they can concentrate on their core business and do what they really enjoy. In a tight employment market, this is an important argument for recruiting and retaining your employees.
You can analyse the performance of your teams in real time
What tools do you have today to identify unbalanced work schedules, too-frequent cancellations, or decreasing on-time service rate?
Yet all these factors can quickly disorganise a team and worsen results.
Thanks to the indicators gathered by most service management software, you can easily detect this type of problem and take the necessary measures to restore and maintain top performance.
Would you like a demo or a free 7-day trial of our service management software? Just leave us your contact details.
Free 7-day trial | No credit card required
Contenu
- What is maintenance schedule?
- Information and data to be gathered
- What is the difference between a maintenance plan and a maintenance schedule?
- The main steps to follow to create a workable maintenance schedule
- 1. Plan preventive maintenance operations
- 2. Keep a safety margin for the unexpected events
- 3. Plan emergency repairs and unforeseen incidents
- 4. Analyse the results to optimise your performance
- Which IT tool should you use to manage your maintenance schedule?
- Excel, the first choice
- Shared calendars
- Maintenance management software
- Route optimisation software
- 5 good reasons to create your maintenance schedule
- You can allocate company resources smarter
- You can manage emergencies and unforeseen events more easily
- You can improve your profitability
- You increase the loyalty of your current technicians
- You can analyse the performance of your teams in real time