The secret of faster, more efficient field service management
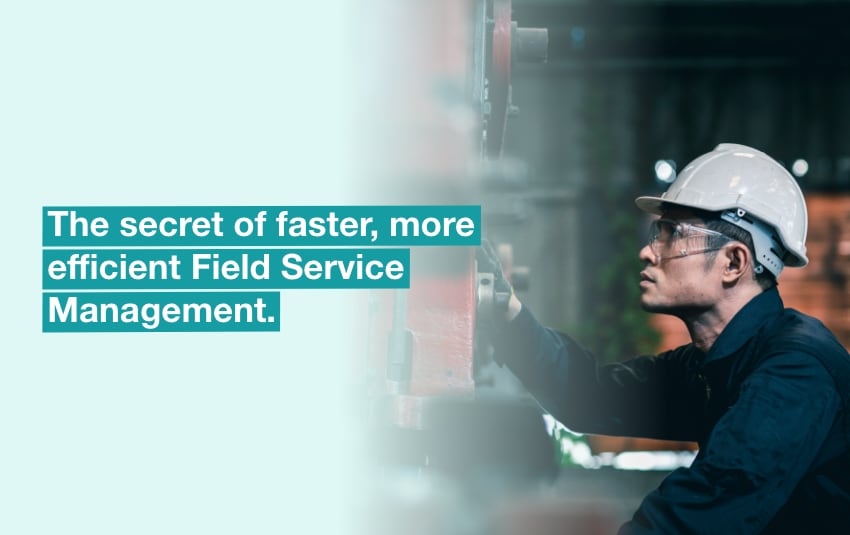
Blog > Field Service > The secret of faster, more efficient field service management
The secret of faster, more efficient field service management
Published on 27 February 2025 • Reading time: 9 min read
How do you combine speed and efficiency in the management of field operations without increasing costs or compromising service quality? This is a major challenge for companies under increasing pressure to meet ever more demanding Service Level Agreements (SLAs). Speeding up response times is no longer enough: the entire process needs to be rethought to improve performance without sacrificing customer satisfaction.
The solution? An intelligent approach, combining route optimisation, artificial intelligence and real-time management. Companies adopting these innovations, like those using AntsRoute, are not just keeping pace: they’re getting ahead of the game.
Table of contents:
- Speed versus efficiency: what’s at stake?
- Route optimisation: the key to fast, efficient management
- Maximise technician productivity without compromising service quality
- Reinventing SLAs: Realistic and transparent commitments
- Technology and automation: the future of field services
Speed versus efficiency: what’s at stake?
When it comes to managing operations in the field, should you give priority to speed or efficiency? On the one hand, customers expect immediate responsiveness. On the other, efficient organisation is essential to keep costs under control and ensure a quality service. But isn’t there a risk of losing efficiency by trying to move too fast?
Speed: an essential but not sufficient criterion
Being fast means being able to respond as quickly as possible to a customer request. But speed isn’t just a question of deadlines:
- Reduce response times: Dispatch a technician as quickly as possible.
- Optimise journeys: Minimise travel time between two work orders.
- Dynamic emergency management: Respond effectively to unforeseen incidents.
But be careful! A rapid response does not guarantee a quality service. A race to speed without structured organisation can lead to excessive costs and a deterioration in service:
- Increased operational costs: More technicians on the road, more overtime, higher fuel consumption, wear and tear on vehicles.
- Sloppy work: Errors, incomplete work, need for a second visit.
- Fatigue among teams: Increased pressure, loss of motivation, increased staff turnover.
Efficiency: the key to profitability and quality
While speed is a key criterion, efficiency depends on optimised resource management. The aim is to guarantee a fast, but well-executed response.
- Distribute work intelligently according to the skills of the technicians.
- Maximise the resolution rate from the first visit, to avoid returns to the worksite.
- Optimise routes to reduce unnecessary journeys and cut costs.
- Use real-time data to adjust operations in the event of unforeseen circumstances.
Note: A well-assigned and well-prepared technician is better than a technician running around.
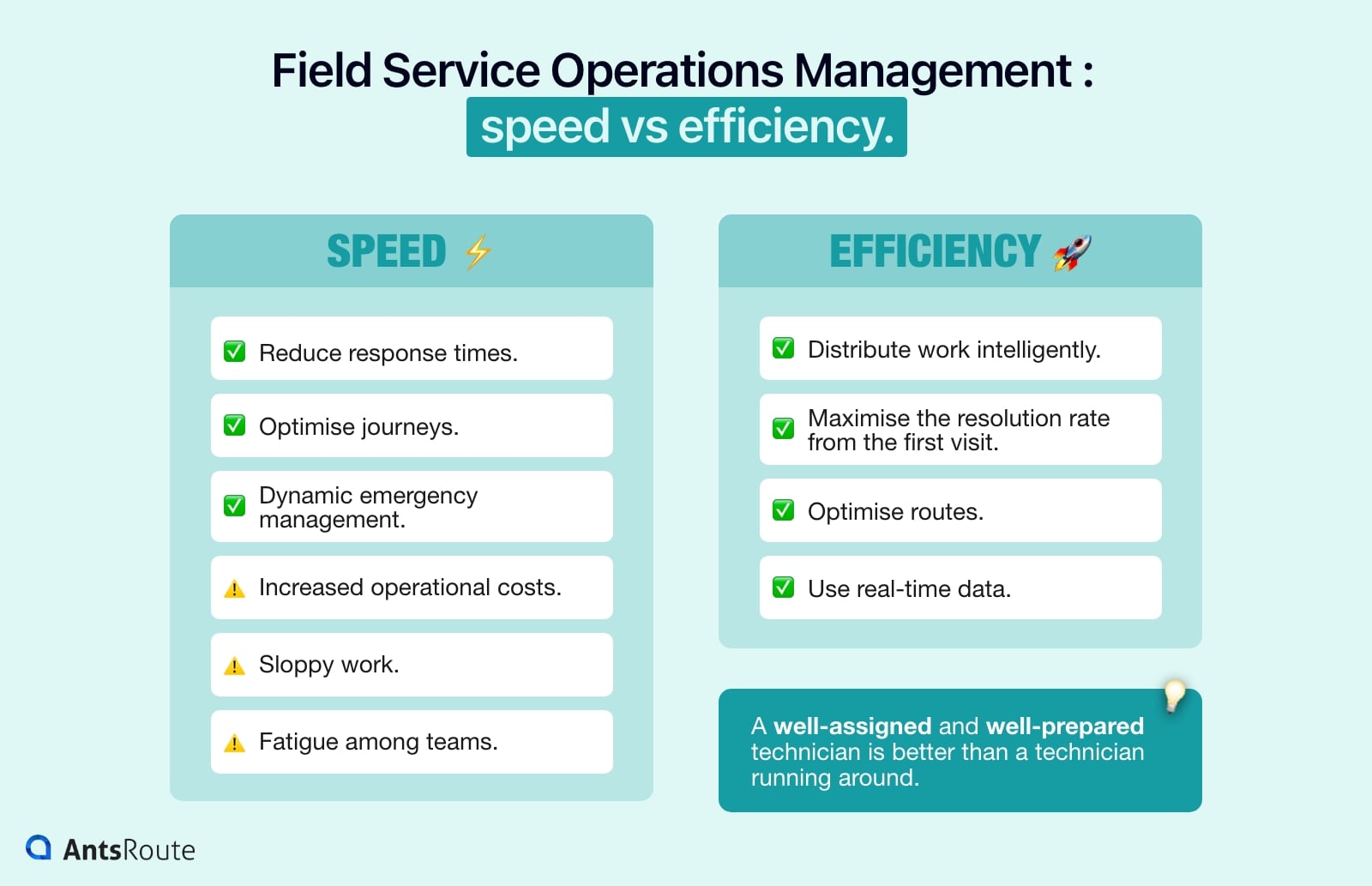
Field service operations management: speed versus efficiency.
Finding the perfect balance between speed and efficiency
The aim is not to choose between speed and efficiency, but to combine them intelligently to achieve optimum management of operations.
- ✔️ Prioritising emergencies without disrupting other tasks.
- ✔️ Using advanced planning software to balance responsiveness and profitability.
- ✔️ Analyse past performance to fine-tune response strategy.
- ✔️ Automate route management, while leaving teams room for manoeuvre.
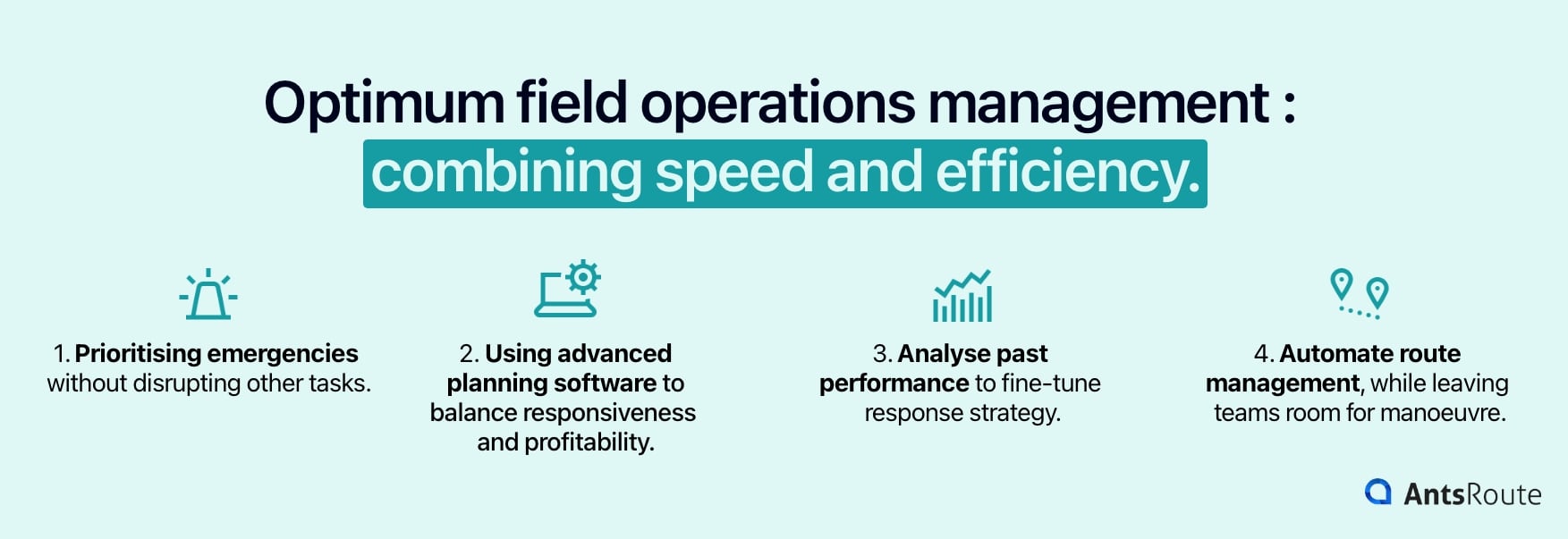
Optimum field service management: combining speed and efficiency.
The impact of SLAs on the performance of field service operations
Service Level Agreements (SLAs) are much more than simple contractual commitments: they define customers’ expectations in terms of responsiveness and quality. When they are well thought out, they help to optimise the organisation of work orders, reduce delays and distribute technicians’ workloads more evenly.
However, over-ambitious SLAs can generate additional costs and put pressure on teams, adversely affecting the quality of field operations. For example, demanding a two-hour response time without taking account of constraints on the ground can lead to longer journeys, more overtime and more errors.
Route optimisation: the key to fast, efficient management
Journeys optimised in real time
Intelligent planning software analyses several parameters in real time to suggest the most efficient route. The result? Fewer unnecessary journeys and more time spent on-site.
- Optimised assignment of tasks to the closest technicians.
- Takes account of traffic and driving conditions to avoid traffic jams.
- Group work in the same area to limit unnecessary journeys.
- Optimise the order in which jobs are carried out, according to schedules and priorities.
Example: By adopting AntsRoute software, Océan-Orange Business Services has enabled its customers to reduce the number of kilometres travelled by their teams by around 20%, resulting in a 35% reduction in social and environmental costs.
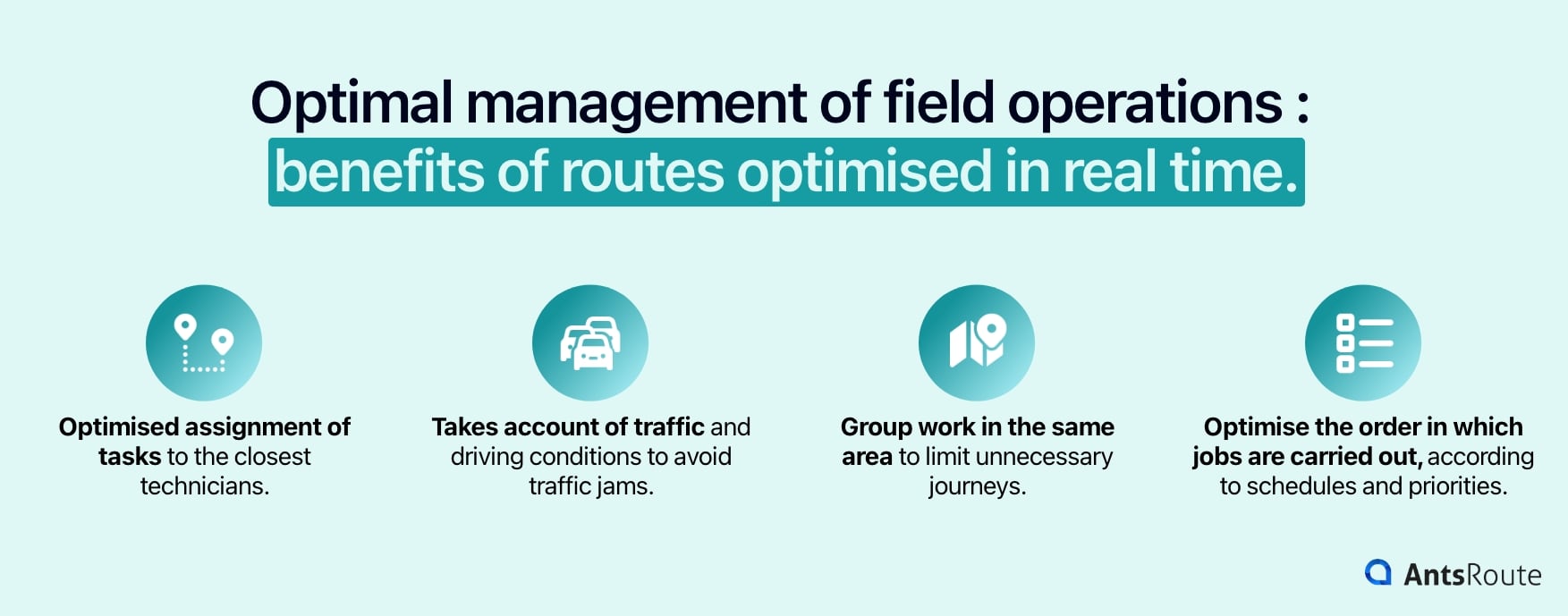
Optimum management of field service operations: The benefits of optimised routes in real time.
Managing the unexpected with real-time data
Even with perfect planning, the unexpected is inevitable: A customer cancels a job at the last minute? A technician gets stuck in a traffic jam? A logistics problem delays an assignment?
The solution? Real-time monitoring. Intelligent management tools enable routes to be adjusted instantly to avoid wasting time.
- Automated reassignment of cancelled jobs.
- Live route recalculation to avoid traffic jams.
- Notifications sent to technicians and customers for better coordination.
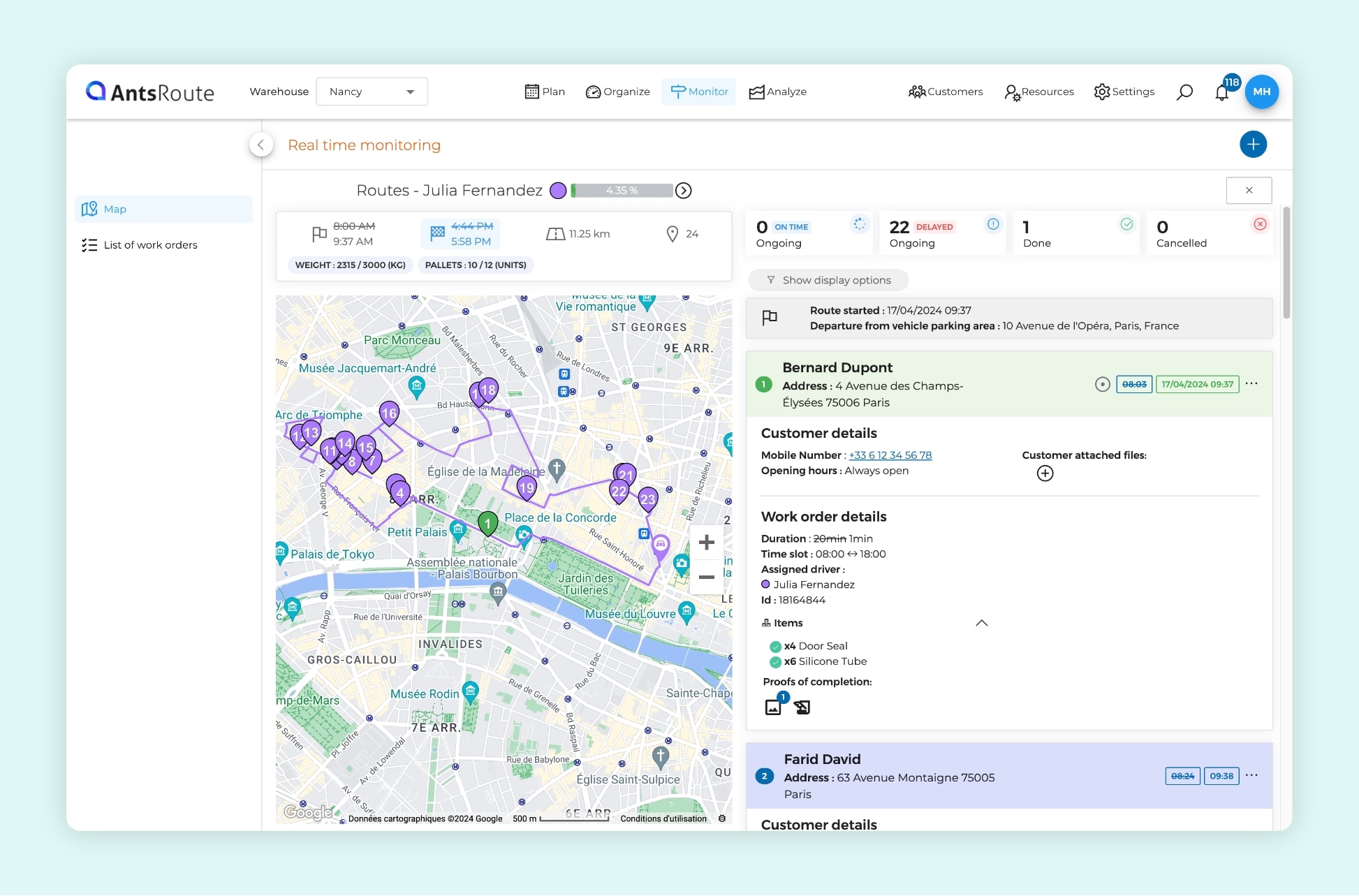
Real-time monitoring of field service routes on AntsRoute.
Anticipating demand using AI and predictive analysis
Artificial intelligence (AI) goes even further by anticipating peaks in demand and future needs to better allocate resources. Thanks to predictive analysis, companies are able to: identify periods of intense activity, adapt the number of technicians available or predict breakdowns or maintenance requirements before they occur.
How does it work?
- AI analyses the history of field services to detect trends and recurring patterns.
- It cross-references this data with external factors (weather, seasonality, local events, etc.).
- It proposes proactive planning: reinforcing teams, reallocating resources and anticipating emergencies.
Automation and flexibility: the role of the human being remains essential
While automation and AI offer many advantages, they should not replace human decision-making.
An algorithm that is too rigid may lack flexibility in the face of exceptional situations. What’s more, AI depends on precise data: an error in information can have an impact on the entire planning process. Some complex operations require human judgement, which AI cannot replace.
The best approach? A hybrid approach, combining technology and human expertise, to ensure efficiency, adaptability and quality of service.
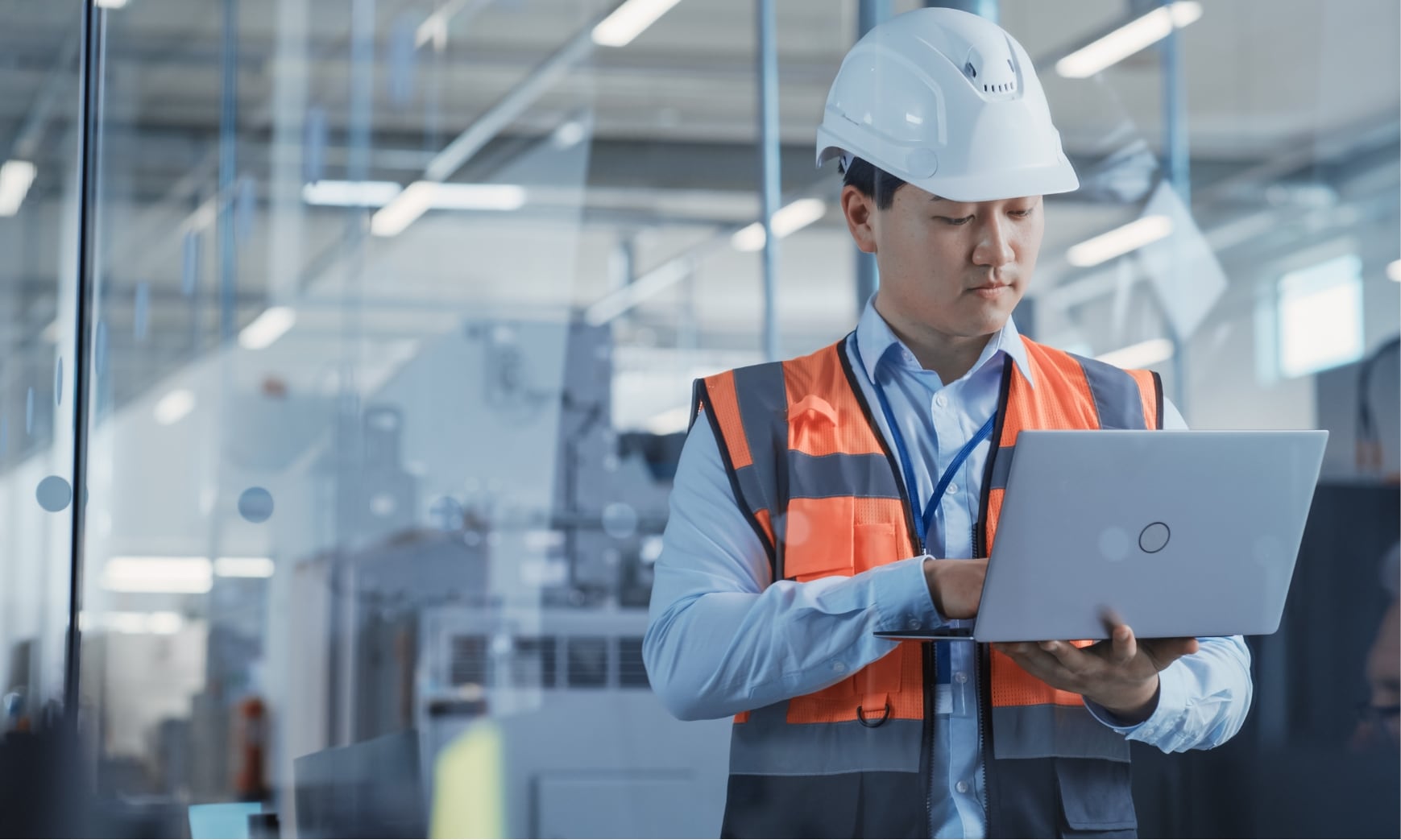
A hybrid approach, combining technology and human expertise, enables effective management of field service operations.
Maximise technician productivity without compromising service quality
Better organisation, better distribution, better anticipation: these are the keys to optimising the work of technicians without overloading them.
Intelligent planning for a more efficient workforce
Poor planning is costly: unnecessary travel, under-used or overworked technicians, poorly managed deadlines… Optimised organisation can reduce these inefficiencies and optimise technicians’ working time.
- Route optimisation: allocate missions according to location and priorities.
- Intelligent distribution of tasks: Assign technicians according to their skills and availability. With AntsRoute, you can classify jobs into several levels:
- Priority: Assigned immediately to the nearest qualified technicians.
- Standard: Planned according to an optimised itinerary.
- Non-urgent: Organised in advance to maximise efficiency without pressure.
- Anticipating unforeseen events: Real-time data can be used to adjust schedules in the event of cancellations or delays.
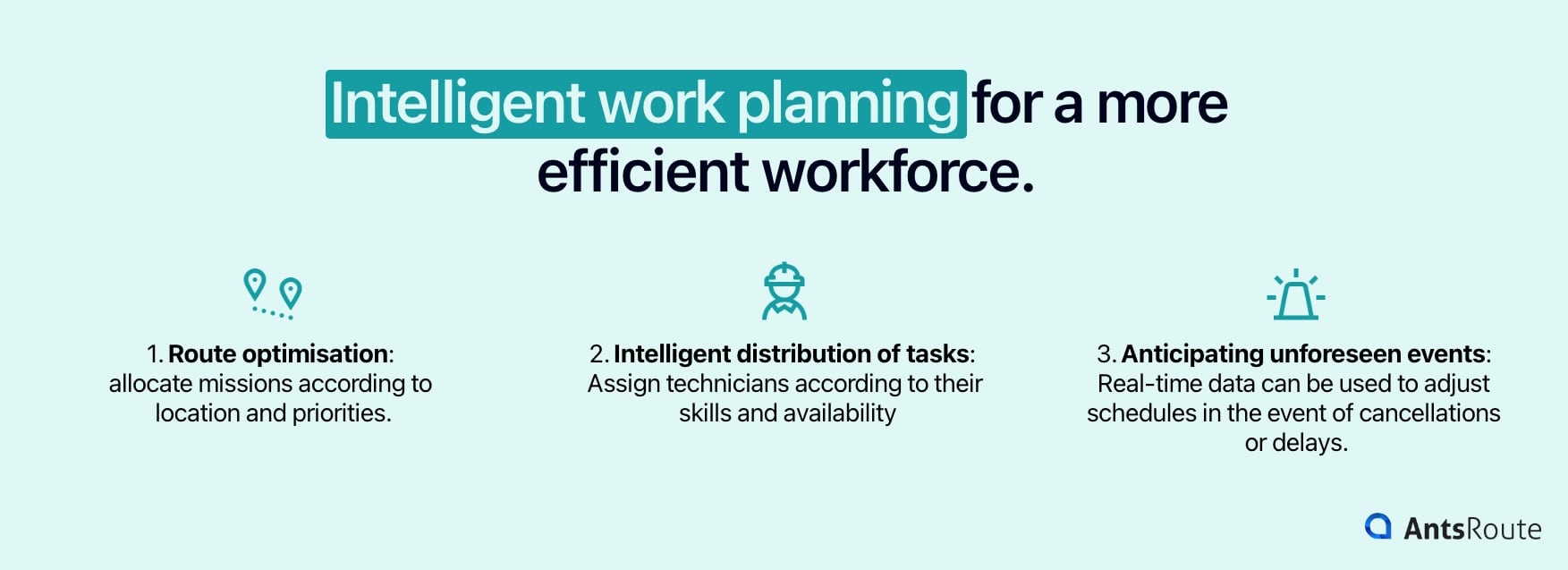
Intelligent scheduling for a more efficient workforce.
Reducing downtime between two operations
Every minute of inactivity is costly. To avoid these slow periods, you can adopt these strategies:
- ✔️ Dynamic planning in real time: Automatic adjustment of routes in the event of cancellations.
- ✔️ Intelligent slot creation: Analysis of service history to better allocate work.
- ✔️ Automated assignment of tasks: Immediate reassignment of a task in the event of unforeseen circumstances.
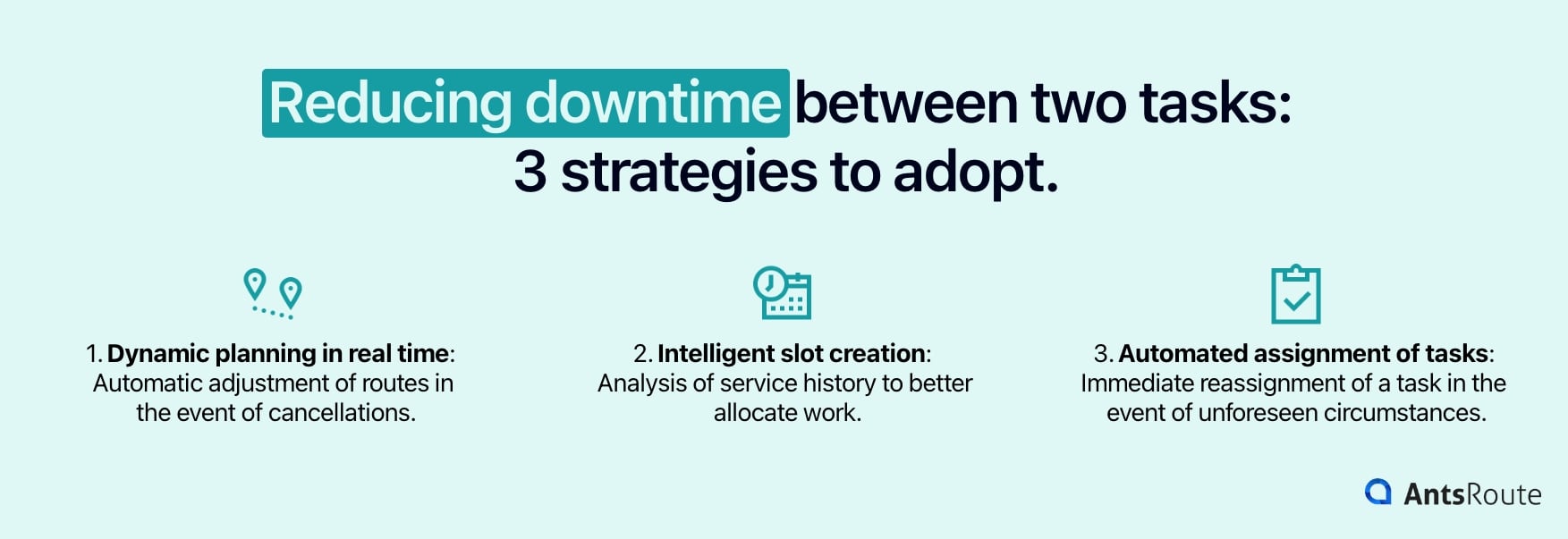
The 3 strategies to adopt to reduce downtime between two field operations.
The importance of matching skills
The wrong technician means wasted time and the risk of incomplete work. Assigning the right job to the right expert guarantees a higher success rate from the very first visit.
- ✔️ Fewer repeat work orders: A qualified technician solves the problem first time.
- ✔️ Optimised working time: Assignments tailored to individual skills.
- ✔️ Team development: Assigning technicians according to their expertise strengthens their commitment and efficiency.
Example: This is the case of the Pôle Équilibre et Santé de Bascharage, which, by adopting AntsRoute, has been able to assign its therapists according to patients’ specific needs. The result? Smoother treatment, time savings and greater profitability.
Reinventing SLAs: Realistic and transparent commitments
Set SLAs in line with actual capacities
A well-defined SLA should neither put pressure on technicians nor disappoint customers. It must be based on concrete data and realistic planning.
- ✔️ Analysis of past performance: What is the average response time according to the type of mission and the constraints on the ground?
- ✔️ Adjusting deadlines according to operational capacity: Objectives must be achievable according to the number of technicians available.
- ✔️ Avoid unrealistic promises: Impossible deadlines lead to stress, delays and a drop in service quality.
- ✔️ Adapt SLAs to the specific nature of your operations: A single commitment for all customers does not take into account distances and the availability of resources.
Rather than imposing a 2-hour response time for everyone, a maintenance company can opt for a more flexible system:
- Urgent operations: Response within 2 hours.
- Standard operations: Response within 24 to 48 hours.
- Planned operations: Integration into optimised routes within 5 days.
Transparent communication to avoid frustration
Customers prefer a realistic deadline to a broken promise. Clear, proactive communication ensures customer satisfaction and better management of response times.
- Inform in advance: Clearly explain the response times and priority levels.
- Real-time monitoring: Allow customers to check the status of their request.
- Automated notifications: Inform the customer in the event of a delay or change to the slot.
- Offer alternatives: Offer a postponement with a specific time slot rather than a vague deadline to avoid the feeling of having to wait a long time.
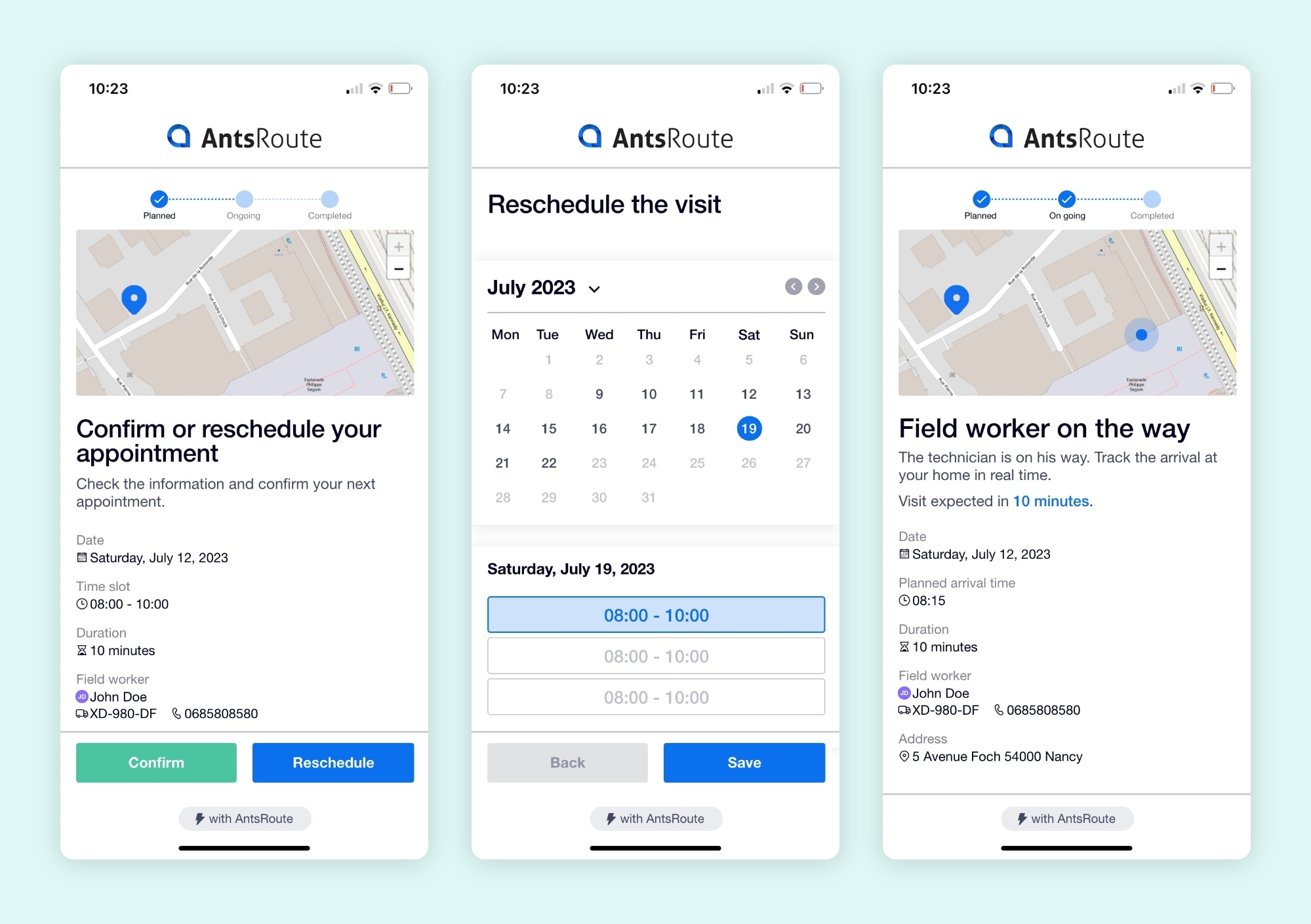
The automated system for notifying customers of AntsRoute.
Technology and automation: the future of field services
Autonomous dispatching and intelligent fleet management
No more manual scheduling! Intelligent dispatching tools, based on AI, analyse several parameters in real time to automatically assign the right job to the right technician.
- Availability and location of technicians: Automatic assignment of tasks to the nearest technician.
- Specific skills: Dispatch the most qualified technician to maximise resolution on the first visit.
- Traffic conditions and constraints in the field: Dynamic adjustment of routes to avoid delays.
- Fleet operational capacity: Intelligent vehicle management to reduce fuel consumption and limit environmental impact.
Predictive maintenance thanks to the IoT : Anticipate rather than suffer
Why wait for a breakdown when you can avoid it? Thanks to the Internet of Things (IoT) and predictive analysis, equipment is continuously monitored, enabling action to be taken before a problem occurs.
How does it work?
- Connected sensors that monitor performance in real time (temperature, vibrations, energy consumption, etc.).
- AI analysis of data to detect anomalies before a breakdown occurs.
- Preventive scheduling of field service operations to avoid costly downtime.
Example: Otis Elevator, a leader in the lift sector, has developed Otis One, an IoT solution enabling it to move from reactive to predictive maintenance. By collecting and analysing data in real time, the company can anticipate breakdowns and reduce the number of emergency repairs.
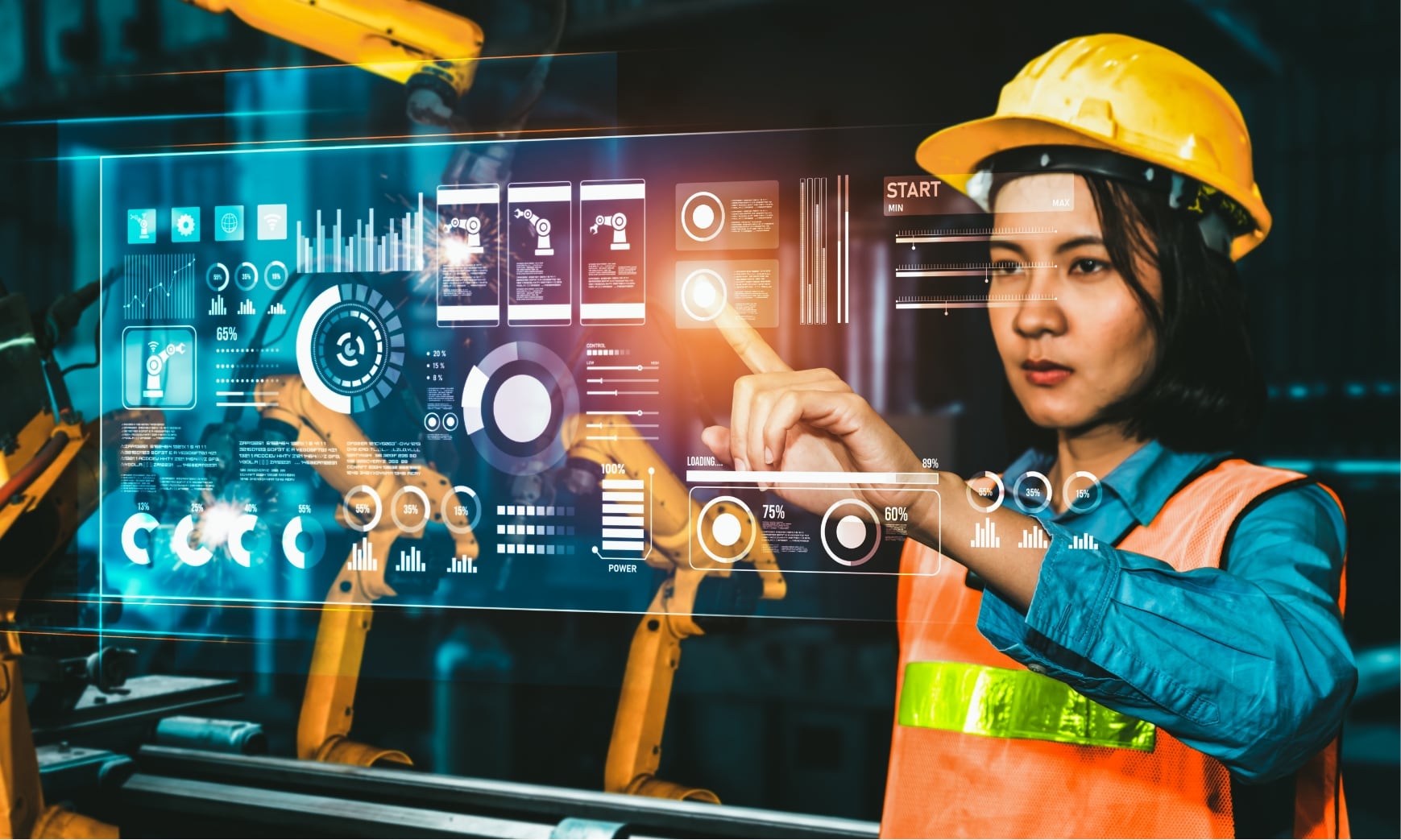
Thanks to the Internet of Things (IoT), equipment is continuously monitored
Drones, AI and augmented reality: the future of field service operations
Emerging technologies are revolutionising the way operations are carried out, making technicians’ work faster, more precise and more efficient.
Drones
- Ultra-fast delivery of spare parts or tools directly to site, reducing waiting time for technicians.
- Remote inspection of hard-to-reach infrastructure ( electrical pylons, roofs, pipelines). Skygauge Robotics estimates that its drones enable inspections to be carried out 5 to 10 times faster than with traditional methods.
Technical assistance by AI
- AI chatbots capable of answering technicians’ technical questions in real time. Kolus reports that the use of AI chatbots can reduce the average time taken to process tickets by 30% and technical trips by 20%, thanks to automated pre-diagnosis.
- Analysis of the symptoms of a breakdown and suggested diagnosis even before the technician arrives on site.
Augmented reality for remote assistance
- Real-time guidance from an expert, who sees what the technician sees via connected glasses.
- Augmented reality display of instructions, making repairs easier even without advanced expertise.
So the aim is not just to speed up field service operations, but to organise them better. So you want to optimise the management of your operations? Find out how AntsRoute can transform your field organisation and improve your profitability. Test it for free for 7 days!
WRITTEN BY
Florine Martin
Florine has been a freelance web copywriter since 2021, writing for a variety of clients in a range of sectors. Since the beginning of 2024, she has been writing articles about logistics for our company, AntsRoute.
Free 7-day trial | No credit card required
Contenu
- Speed versus efficiency: what’s at stake?
- Speed: an essential but not sufficient criterion
- Efficiency: the key to profitability and quality
- Finding the perfect balance between speed and efficiency
- The impact of SLAs on the performance of field service operations
- Route optimisation: the key to fast, efficient management
- Journeys optimised in real time
- Managing the unexpected with real-time data
- Anticipating demand using AI and predictive analysis
- Automation and flexibility: the role of the human being remains essential
- Maximise technician productivity without compromising service quality
- Intelligent planning for a more efficient workforce
- Reducing downtime between two operations
- The importance of matching skills
- Reinventing SLAs: Realistic and transparent commitments
- Set SLAs in line with actual capacities
- Transparent communication to avoid frustration
- Technology and automation: the future of field services
- Autonomous dispatching and intelligent fleet management
- Predictive maintenance thanks to the IoT : Anticipate rather than suffer
- Drones, AI and augmented reality: the future of field service operations
- Drones
- Technical assistance by AI
- Augmented reality for remote assistance